Environment-friendly flame-retardant polyvinyl chloride cable sheath material and preparation method thereof
A technology of flame retardant PVC and cable sheathing materials, applied in the direction of insulated cables, cables, circuits, etc., can solve problems such as toxic and corrosive smoke, fire fighting and loss of people's lives and properties
- Summary
- Abstract
- Description
- Claims
- Application Information
AI Technical Summary
Problems solved by technology
Method used
Image
Examples
Embodiment 1
[0022] First put (the following are parts by weight) 100 parts of polyvinyl chloride and 6 parts of stabilizer into a high-speed mixer for high-speed mixing. When the temperature rises to 60°C, add 40 parts of plasticizer UN488, 6 parts of long-chain chlorine Paraffin wax and 4 parts of epoxidized soybean oil, when the temperature reaches 80°C, add 5 parts of antimony trioxide, 8 parts of zinc borate hydrate and 12 parts of active aluminum hydroxide, when the temperature reaches 90°C, add 20 parts of active weight High quality calcium carbonate and 20 parts of nano calcium carbonate, when the temperature reaches 100°C, add 0.6 part of stearic acid and 0.6 part of butyl stearate, when the temperature reaches 110°C, stop high speed mixing. Unload the material into the low-speed mixer for low-speed mixing and cooling, unload the cooled material into the hopper elevator, add it to the twin-screw extruder for mixing, extrude, granulate and pack.
Embodiment 2
[0024] First put (the following are parts by weight) 100 parts of polyvinyl chloride and 5 parts of stabilizer into a high-speed mixer for high-speed mixing. When the temperature rises to 60°C, add 35 parts of plasticizer UN488, 4 parts of long-chain chlorine Paraffin wax and 3 parts of epoxy soybean oil, when the temperature reaches 80 ℃, add 6 parts of antimony trioxide, 10 parts of hydrated zinc borate and 14 parts of active aluminum hydroxide, when the temperature reaches 90 ℃, add 15 parts of active weight High quality calcium carbonate and 25 parts of nano calcium carbonate, when the temperature reaches 100°C, add 0.5 part of stearic acid and 0.5 part of butyl stearate, when the temperature reaches 110°C, stop high-speed mixing. Unload the material into the low-speed mixer for low-speed mixing and cooling, unload the cooled material into the hopper elevator, add it to the twin-screw extruder for mixing, extrude, granulate and pack.
Embodiment 3
[0026] First put (the following are parts by weight) 100 parts of polyvinyl chloride and 7 parts of stabilizer into a high-speed mixer for high-speed mixing. When the temperature rises to 60 ° C, add 45 parts of plasticizer UN488, 10 parts of long-chain chlorine Paraffin wax and 5 parts of epoxidized soybean oil, when the temperature reaches 80°C, add 4 parts of antimony trioxide, 6 parts of zinc borate hydrate and 10 parts of active aluminum hydroxide, when the temperature reaches 90°C, add 25 parts of active weight High-quality calcium carbonate and 30 parts of nano-calcium carbonate, when the temperature reaches 100 ° C, add 0.7 parts of stearic acid and 0.7 parts of butyl stearate, when the temperature reaches 110 ° C, stop high-speed mixing. Unload the material into the low-speed mixer for low-speed mixing and cooling, unload the cooled material into the hopper elevator, add it to the twin-screw extruder for mixing, extrude, granulate and pack.
PUM
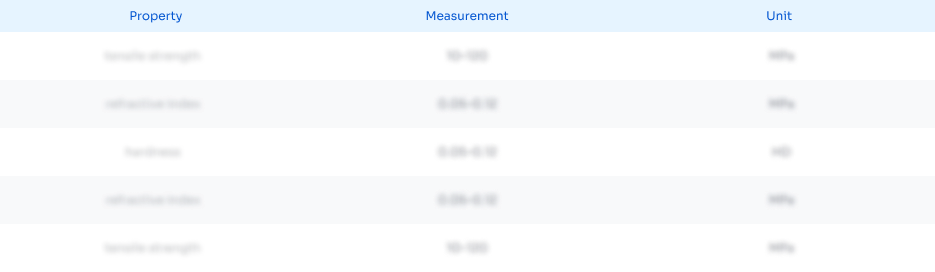
Abstract
Description
Claims
Application Information

- Generate Ideas
- Intellectual Property
- Life Sciences
- Materials
- Tech Scout
- Unparalleled Data Quality
- Higher Quality Content
- 60% Fewer Hallucinations
Browse by: Latest US Patents, China's latest patents, Technical Efficacy Thesaurus, Application Domain, Technology Topic, Popular Technical Reports.
© 2025 PatSnap. All rights reserved.Legal|Privacy policy|Modern Slavery Act Transparency Statement|Sitemap|About US| Contact US: help@patsnap.com