Large spiral low-order lignite quality improving system
A spiral, lignite technology, applied in the field of dry distillation system, can solve the problems affecting the stable operation of the system, uneven quality of semi-coke, uneven heating of coal, and achieves compact structure, low particle size requirements, and small footprint. Effect
- Summary
- Abstract
- Description
- Claims
- Application Information
AI Technical Summary
Problems solved by technology
Method used
Image
Examples
Embodiment Construction
[0024] see figure 1 The system of the present invention includes a horizontally arranged spiral heat exchanger, and the two ends of the spiral heat exchanger are respectively connected with the combustion chamber 19 and the dust removal device. The spiral heat exchanger is the main device of the system. The spiral heat exchanger is composed of a cylindrical jacket 17 with gradually shrinking diameter on both sides, a rotating shaft 15 and a motor 11 arranged in the jacket, and the motor drives the rotating shaft to rotate. A helical blade 14 is arranged in the axial direction of the rotating shaft, and the outer casing wall, the rotating shaft and the helical blade are all hollow structures, and the two ends of the helical blade communicate with the cavity in the rotating shaft to form a spiral flue gas channel. The inlet ends of the outer casing wall cavity and the rotating shaft cavity are connected with the combustion chamber, and the outlet ends of the outer casing wall ca...
PUM
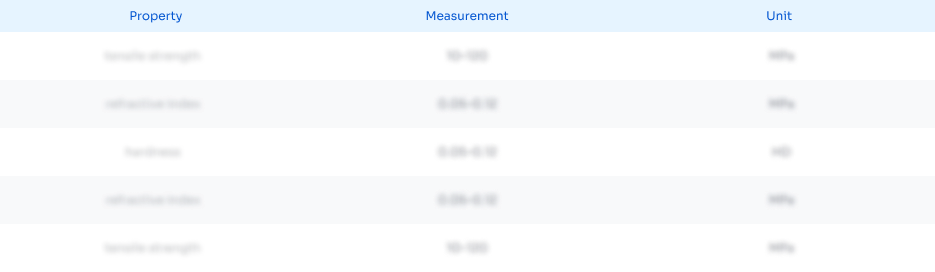
Abstract
Description
Claims
Application Information

- R&D Engineer
- R&D Manager
- IP Professional
- Industry Leading Data Capabilities
- Powerful AI technology
- Patent DNA Extraction
Browse by: Latest US Patents, China's latest patents, Technical Efficacy Thesaurus, Application Domain, Technology Topic, Popular Technical Reports.
© 2024 PatSnap. All rights reserved.Legal|Privacy policy|Modern Slavery Act Transparency Statement|Sitemap|About US| Contact US: help@patsnap.com