Alloy material for ring gear for automobile synchronizer
An alloy material and synchronizer technology, which is applied in the field of metal material alloying, can solve the problems of different crystal structure and crystal morphology, different matrix strength and wear resistance, and impact on the life of the gear ring, so as to achieve good service performance and improve cutting performance. , the effect of long service life
- Summary
- Abstract
- Description
- Claims
- Application Information
AI Technical Summary
Problems solved by technology
Method used
Examples
Embodiment 1
[0025]Put Cu with a mass percentage of 50% into a power frequency furnace for smelting, and after the copper starts to soften, cover a layer of charcoal on the copper surface. The amount of charcoal is 15-25kg per ton of copper. The melting temperature is 1180-1200°C. Add 4.3% Ni by mass percentage to the molten copper liquid, so that metallic nickel can be dissolved into the copper liquid through alloying. After Ni is melted, 1.1% Fe by mass percentage is added to the molten copper liquid, so that metallic iron is dissolved into the copper liquid through alloying. Add 3.5% Al and 13% Cu by mass percentage to the copper liquid; use the heat of dissolution of aluminum to melt the cold material copper to achieve the purpose of reducing energy consumption and metal burning loss. After the added Al and Cu are melted, add Zn with a mass percentage of 20% to the molten copper, and the melting temperature is 1160-1180°C; if aluminum is added first and then zinc is added, aluminum c...
Embodiment 2
[0030] Put Cu with a mass percentage of 45% into a power frequency furnace for smelting. After the copper starts to soften, cover a layer of charcoal on the copper surface. The amount of charcoal is 15-25kg per ton of copper. The melting temperature is 1180-1200°C. Add 1.1% Ni by mass percentage to the molten copper liquid to dissolve metallic nickel into the copper liquid through alloying. After Ni is melted, 0.7% Fe by mass is added to the molten copper to dissolve metallic iron into the molten copper through alloying. 2.0% Al and 11% Cu are added to the copper liquid; the heat of dissolution of aluminum is used to melt the cold material copper to achieve the purpose of reducing energy consumption and metal burning loss. After the added Al and Cu are melted, 38 mass percent Zn is added to the molten copper, and the melting temperature is 1060-1100°C. After the metal Zn is melted, add Cu-Mn and Cu-Ti intermediate alloys to the copper liquid, so that the mass percentages of...
Embodiment 3
[0035] Put Cu with a mass percentage of 50% into a power frequency furnace for smelting, and after the copper starts to soften, cover a layer of charcoal on the copper surface. The amount of charcoal is 15-25kg per ton of copper. The melting temperature is 1180-1200°C. Add 1.1% Ni by mass percentage to the molten copper liquid to dissolve metallic nickel into the copper liquid through alloying. After Ni is melted, 1.2% Fe by mass percentage is added to the molten copper liquid, so that metallic iron is dissolved into the copper liquid through alloying. Add 4.0% Al and 13% Cu to the molten copper; after the added Al and Cu are melted, add 28% Zn to the molten copper at a melting temperature of 1120-1170°C. After the metal Zn is melted, add Cu-Mn and Cu-Ti intermediate alloys to the copper liquid, so that the mass percentages of Mn and Ti in the finished alloy are 4% and 0.9%; add Si to the copper liquid to make the Si in the finished alloy The mass percentage is 0.5%; add Sn...
PUM
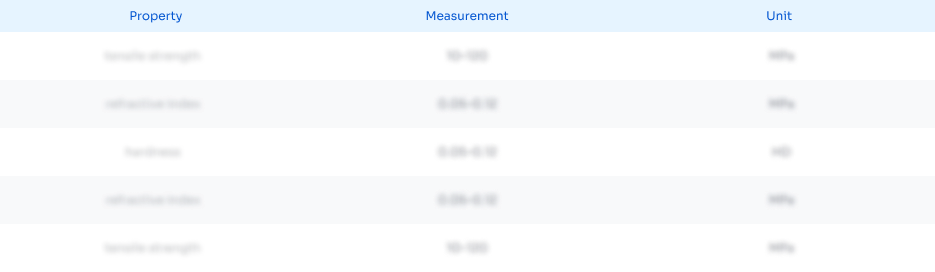
Abstract
Description
Claims
Application Information

- R&D
- Intellectual Property
- Life Sciences
- Materials
- Tech Scout
- Unparalleled Data Quality
- Higher Quality Content
- 60% Fewer Hallucinations
Browse by: Latest US Patents, China's latest patents, Technical Efficacy Thesaurus, Application Domain, Technology Topic, Popular Technical Reports.
© 2025 PatSnap. All rights reserved.Legal|Privacy policy|Modern Slavery Act Transparency Statement|Sitemap|About US| Contact US: help@patsnap.com