Method and device for rapid high-temperature heating of plates
A high-temperature heating and heating method technology, which is applied in the direction of measuring devices, heat treatment furnaces, and analytical materials, can solve the problems that the heating furnace occupies a large space, cannot reach a high temperature above 900°C, and is easy to be oxidized, and achieves a compact structure of the device. Easy to make, stable and reliable effect
- Summary
- Abstract
- Description
- Claims
- Application Information
AI Technical Summary
Problems solved by technology
Method used
Image
Examples
Embodiment 1
[0031] Such as Figure 5a , as shown in 5b and 5c, bend the induction coil 5 into a rectangular frame of 220*220*50mm to ensure the uniformity of heating, a total of 30 turns, and the specific parameters are shown in Table 1.
[0032] Table 1 Induction coil parameter list
[0033]
[0034] Such as Figure 1-4 As shown, the induction coil 5 bent into a rectangular frame is fixed and packaged with cement to form a box-shaped heating chamber with one side open, and the positions required for the installation of the protective gas charging port 3 and the thermocouple installation hole 4 are fixed. After the cement is cured , that is, the cement heating chamber 2 is formed. The graphite inner cavity 1 is placed in the center of the cement heating cavity 2, and a gap of 3 mm is left, which is fixed with cement slurry.
[0035] Pass the inert gas helium into the protective gas filling hole 3, drive away the air in the cement heating chamber 2, and prevent the sample from being ...
Embodiment 2
[0037] Such as Figure 5a , 5b, 5c, the induction coil 5 is bent into a rectangular frame of 500mm*500mm*80mm to ensure the uniformity of heating, a total of 80 turns.
[0038] Such as Figure 1-4 As shown, the induction coil 5 bent into a rectangular frame is fixed and packaged with cement to form a box-shaped heating chamber with one side open, and the positions required for the installation of the protective gas charging port 3 and the thermocouple installation hole 4 are fixed. After the cement is cured , that is, the cement heating chamber 2 is formed. The graphite inner cavity 1 is placed in the center of the cement heating cavity 2, and a gap of 8mm is left, and is fixed with cement slurry.
[0039]Pass the inert gas helium into the protective gas filling hole 3, drive away the air in the cement heating chamber 2, and prevent the sample from being over-oxidized at high temperature. Install it in the thermal couple installation hole 4, and connect the thermostat; conn...
Embodiment 3
[0041] Such as Figure 5a , As shown in 5b and 5c, the induction coil 5 is bent into a rectangular frame of 400mm*400mm*65mm to ensure the uniformity of heating, with a total of 60 turns.
[0042] Such as Figure 1-4 As shown, the induction coil 5 bent into a rectangular frame is fixed and packaged with cement to form a box-shaped heating chamber with one side open, and the positions required for the installation of the protective gas charging port 3 and the thermocouple installation hole 4 are fixed. After the cement is cured , that is, the cement heating chamber 2 is formed. The graphite inner cavity 1 is placed in the center of the cement heating cavity 2, and a gap of 5mm is left, and is fixed with cement slurry.
[0043] Pass the inert gas helium into the protective gas filling hole 3, drive away the air in the cement heating chamber 2, and prevent the sample from being over-oxidized at high temperature. Install it in the thermal couple installation hole 4, and connect...
PUM
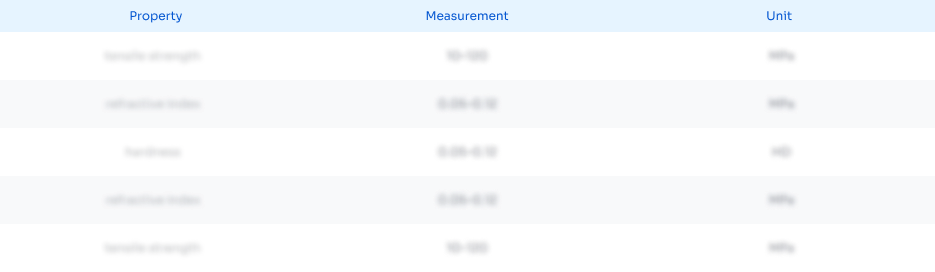
Abstract
Description
Claims
Application Information

- Generate Ideas
- Intellectual Property
- Life Sciences
- Materials
- Tech Scout
- Unparalleled Data Quality
- Higher Quality Content
- 60% Fewer Hallucinations
Browse by: Latest US Patents, China's latest patents, Technical Efficacy Thesaurus, Application Domain, Technology Topic, Popular Technical Reports.
© 2025 PatSnap. All rights reserved.Legal|Privacy policy|Modern Slavery Act Transparency Statement|Sitemap|About US| Contact US: help@patsnap.com