Method for preparing waste recovered graphite powder into graphene
A graphene and graphite powder technology, applied in the field of nanomaterials, can solve the problems of long cycle, environmental pollution and high production cost, and achieve the effects of low cost, huge environmental benefit and short preparation cycle
- Summary
- Abstract
- Description
- Claims
- Application Information
AI Technical Summary
Problems solved by technology
Method used
Image
Examples
Embodiment 1
[0036] 1. Graphite mixed with concentrated sulfuric acid
[0037] First, add 1.0g of graphite powder and 20ml of 98% concentrated sulfuric acid into the reactor and stir to make them evenly mixed. At the same time, use a cooling device (ice bath) to keep the reactor at a low temperature.
[0038] 2. Add potassium permanganate
[0039] After mixing evenly, slowly (very slowly, the temperature will rise sharply during heating) add 3.5g potassium permanganate to the above reaction kettle, and at the same time stir the above solution with a mechanical stirrer at high speed, so that the potassium permanganate can be mixed with the above solution Full contact. During the addition process, use an external cooling device (ice bath) to keep the temperature of the reaction solution in the kettle below 20 degrees Celsius. At this point the solution turned from black to dark green. After the addition was complete, the temperature of the solution was raised to 35 degrees Celsius using a...
Embodiment 2
[0049] 1. Graphite mixed with concentrated sulfuric acid
[0050] First, add 1.0g of graphite powder and 50ml of 98% concentrated sulfuric acid into the reactor and stir to make them evenly mixed. At the same time, use a cooling device (ice bath) to keep the reactor at a low temperature.
[0051] 2. Add potassium permanganate
[0052] After mixing evenly, slowly (very slowly, the temperature will rise sharply during heating) add 4.0g potassium permanganate to the above reaction kettle, and at the same time stir the above solution with a mechanical stirrer at high speed, so that the potassium permanganate can be mixed with the above solution Full contact. During the addition process, use external cooling equipment (circulating water cooling) to keep the temperature of the reaction solution in the kettle below 20 degrees Celsius. At this point the solution turned from black to dark green. After the addition was complete, the temperature of the solution was raised to 35 degree...
Embodiment 3
[0062] 1. Graphite mixed with concentrated sulfuric acid
[0063] First, add 1.0g of graphite powder and 100ml of 98% concentrated sulfuric acid into the reactor and stir to make them evenly mixed. At the same time, use a cooling device (ice bath) to keep the reactor at a low temperature.
[0064] 2. Add potassium permanganate
[0065] After mixing evenly, slowly (very slowly, the temperature will rise sharply during heating) add 5.0g potassium permanganate into the above reaction kettle, and at the same time stir the above solution with a mechanical stirrer at high speed, so that the potassium permanganate can be mixed with the above solution Full contact. During the addition process, use external cooling equipment (circulating water cooling) to keep the temperature of the reaction solution in the kettle below 20 degrees Celsius. At this point the solution turned from black to dark green. After the addition was complete, the temperature of the solution was raised to 35 ...
PUM
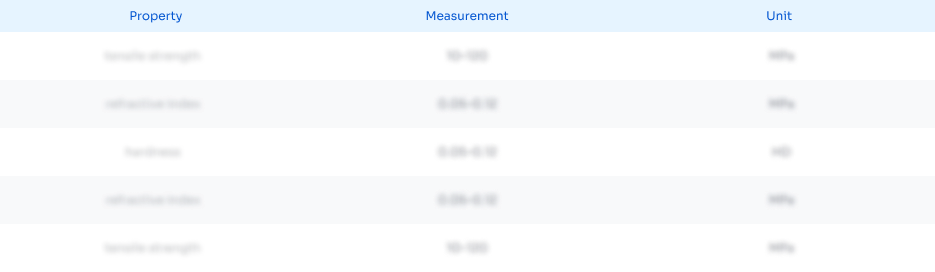
Abstract
Description
Claims
Application Information

- R&D
- Intellectual Property
- Life Sciences
- Materials
- Tech Scout
- Unparalleled Data Quality
- Higher Quality Content
- 60% Fewer Hallucinations
Browse by: Latest US Patents, China's latest patents, Technical Efficacy Thesaurus, Application Domain, Technology Topic, Popular Technical Reports.
© 2025 PatSnap. All rights reserved.Legal|Privacy policy|Modern Slavery Act Transparency Statement|Sitemap|About US| Contact US: help@patsnap.com