Conical surface grinding method
A conical surface and grinding technology, which is applied in the field of high surface precision grinding of outer conical surface, can solve the problems of grinding wheel wear, accelerated grinding wheel wear, and non-constant contact width.
- Summary
- Abstract
- Description
- Claims
- Application Information
AI Technical Summary
Problems solved by technology
Method used
Image
Examples
Embodiment Construction
[0033]The specific implementation manner of the present invention will be described in detail below in combination with the technical scheme and accompanying drawings. The inner radius of the conical surface to be processed is 100 mm, the outer radius is 150 mm, the radial profile inclination is 0.06 radians, and the material is pressureless sintered silicon carbide. The invention is realized by using a cup-shaped grinding wheel, a rotary table, a linear moving platform and a distance adjustment mechanism. The cup-shaped grinding wheel is installed on the ultra-precision air-bearing electric spindle. The abrasive grains used for the cup-shaped grinding wheel are diamonds, the particle size is 1000#, the middle diameter of the cup-shaped grinding wheel is 350 mm, and the width of the grinding surface of the cup-shaped grinding wheel is 3 mm. The axial runout and radial runout of the ultra-precision air bearing electric spindle are less than 0.05 microns, and the ultra-precision...
PUM
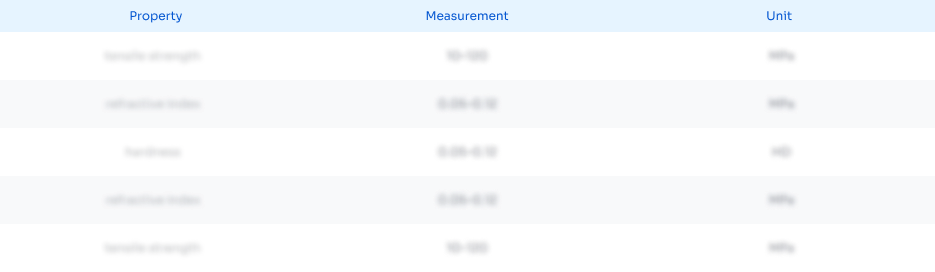
Abstract
Description
Claims
Application Information

- R&D
- Intellectual Property
- Life Sciences
- Materials
- Tech Scout
- Unparalleled Data Quality
- Higher Quality Content
- 60% Fewer Hallucinations
Browse by: Latest US Patents, China's latest patents, Technical Efficacy Thesaurus, Application Domain, Technology Topic, Popular Technical Reports.
© 2025 PatSnap. All rights reserved.Legal|Privacy policy|Modern Slavery Act Transparency Statement|Sitemap|About US| Contact US: help@patsnap.com