Multi-stage spray reaction tower
A spray reaction and reaction chamber technology, applied in the field of reaction towers, can solve the problems of low gas-liquid reaction efficiency, increase the load of the mist eliminator, blockage of the mist eliminator, etc. The effect of increasing the area and reducing the lift resistance
- Summary
- Abstract
- Description
- Claims
- Application Information
AI Technical Summary
Problems solved by technology
Method used
Image
Examples
Embodiment 1
[0043] Embodiment 1: The circular multi-stage spray reaction tower whose vertical partition is a vertical plate
[0044] See Figure 1~Figure 6 , the cross-section of the tower body 9 of the circular multi-stage spray reaction tower is circular. see Figure 1~Figure 6 , the liquid level 7 of the tower kettle of the tower body 9 has a set height, and above the liquid level 7 is the reaction zone. The vertical partitions include high-position partitions m, m', low-position partitions n and full partitions k, all of which are vertical plates consistent with the axial direction of the tower body 9. The reaction zone is divided into four fan-shaped reaction chambers with numbers 1, 2, 3, and 4 respectively by high-position partition m, low-position partition n, and high-position partition m' starting from full partition k ( figure 2 ). The first-stage reaction chamber 1 is adjacent to the end-stage reaction chamber 4, and the two are separated by a full partition k. The lower ...
Embodiment 2
[0046] Embodiment 2: the circular multi-stage spray reaction tower that the longitudinal partition is a vertical plate and
[0047] See Figure 8 , and see Figure 9~Figure 13 , the longitudinal partitions from the first-stage reaction chamber 1 to the final-stage reaction chamber 4 are alternately arranged as inclined plates and vertical plates, that is, the full partition k, the high-position partition m, the low-position partition n, and the high-position partition m 'Slanted slabs, vertical slabs, slanted slabs, and vertical slabs in sequence, the inclination angle α between each slanted slab and the tower body 9 is 5~30° (see Figure 10 , 12 ), it can be seen from the figure that from the first stage to the last stage, the radial distances of the gas inlet ends of the reaction chambers of each stage are larger than the radial distances of the gas outlet ends of the reaction chambers of the same stage. Its advantages are: the gas inlet cross-sectional area of the reac...
Embodiment 3
[0049] Square multi-stage spray reaction tower
[0050] Such as Figure 14 , the cross-section of the tower body 9 is a square. The reaction area is divided into four triangular reaction chambers with numbers 1, 2, 3, and 4 by the high-position partition m, the low-position partition n, and the high-position partition m' sequentially from the full partition k, and the liquid phase material atomization nozzle 8 are respectively installed on the wall of the tower body corresponding to each reaction chamber 1, 2, 3, 4 in the way of radial injection. All the other structures are the same as in Embodiment 1, and are omitted.
PUM
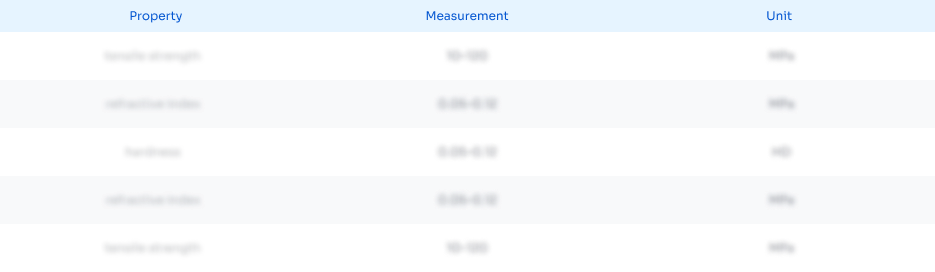
Abstract
Description
Claims
Application Information

- R&D
- Intellectual Property
- Life Sciences
- Materials
- Tech Scout
- Unparalleled Data Quality
- Higher Quality Content
- 60% Fewer Hallucinations
Browse by: Latest US Patents, China's latest patents, Technical Efficacy Thesaurus, Application Domain, Technology Topic, Popular Technical Reports.
© 2025 PatSnap. All rights reserved.Legal|Privacy policy|Modern Slavery Act Transparency Statement|Sitemap|About US| Contact US: help@patsnap.com