Preparation method of delafossite type copper aluminum oxide infrared transparent conductive film
A transparent conductive film, infrared technology, applied in metal material coating process, vacuum evaporation plating, coating, etc., can solve the problems of opacity, achieve good transmittance, improve film quality, and stabilize deposition rate.
- Summary
- Abstract
- Description
- Claims
- Application Information
AI Technical Summary
Problems solved by technology
Method used
Image
Examples
Embodiment 1
[0030] (1) Cleaning of the substrate
[0031] Cleaning of silicon (111) substrates: Clean with acetone solution (analytical grade) in an ultrasonic cleaner for 15 minutes at normal temperature and pressure, then soak in HF for 15 minutes, and finally rinse with deionized water for 5 minutes.
[0032] Cleaning of the sapphire substrate: Clean in an ultrasonic cleaner with acetone solution (analytical grade) for 15 minutes at normal temperature and pressure, then clean with an ethanol solution (analytic grade) in an ultrasonic cleaner for 15 minutes, and finally rinse with deionized water for 5 minutes.
[0033] The two kinds of substrates were dried and placed in the sputtering chamber, where the thin films grown on the silicon substrates were used to test the structure and conductivity of the samples (such as Figure 4 and Figure 5 ), the film grown on the quartz substrate is used to measure the transmittance of the film (such as Figure 6 );
[0034] (2)CuAlO 2 film grow...
Embodiment 2
[0039] (1) Cleaning of the substrate
[0040] Cleaning of silicon (111) substrates: Clean with acetone solution (analytical grade) in an ultrasonic cleaner for 15 minutes at normal temperature and pressure, then soak in HF for 15 minutes, and finally rinse with deionized water for 5 minutes.
[0041] Cleaning of the sapphire substrate: Clean in an ultrasonic cleaner with acetone solution (analytical grade) for 15 minutes at normal temperature and pressure, then clean with an ethanol solution (analytic grade) in an ultrasonic cleaner for 15 minutes, and finally rinse with deionized water for 5 minutes.
[0042] Dry the two substrates and put them into the sputtering chamber, where the thin film grown on the silicon substrate is used to test the structure and conductivity of the sample, and the thin film grown on the quartz substrate is used to measure the transmittance of the thin film;
[0043] (2)CuAlO 2 film growth
[0044] The process is carried out in a high-vacuum multi...
PUM
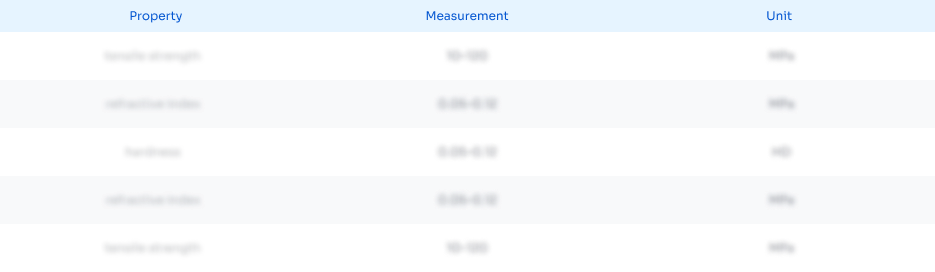
Abstract
Description
Claims
Application Information

- R&D
- Intellectual Property
- Life Sciences
- Materials
- Tech Scout
- Unparalleled Data Quality
- Higher Quality Content
- 60% Fewer Hallucinations
Browse by: Latest US Patents, China's latest patents, Technical Efficacy Thesaurus, Application Domain, Technology Topic, Popular Technical Reports.
© 2025 PatSnap. All rights reserved.Legal|Privacy policy|Modern Slavery Act Transparency Statement|Sitemap|About US| Contact US: help@patsnap.com