Oxidative desulfurization method for rare earth polyacid and ionic liquid extraction catalysis fuel oil
An ionic liquid, rare earth polyacid technology, applied in the direction of refining with oxygenated compounds, can solve the problems of increasing equipment investment and operating costs, not being widely promoted, and reducing the octane number of oil products, achieving easy recycling, The effect of short reaction time and high conversion rate
- Summary
- Abstract
- Description
- Claims
- Application Information
AI Technical Summary
Problems solved by technology
Method used
Image
Examples
Embodiment 1
[0020] 1. Preparation of simulated fuel oil:
[0021] Take 1.4662g (7.793mmol, 98%) of DBT and dissolve it in n-octane to prepare 250mL of simulated fuel oil with a sulfur content of 1000ppm.
[0022] 2. Catalytic oxidation desulfurization experiment:
[0023] 26.5mg Na 9 wxya 10 o 36 32H 2 O, 0.05mL 30wt%H 2 o 2 , 1mL ionic liquid [BMIM]BF 4 , 5mL simulated fuel oil was added to a 50mL double-necked round-bottom flask in turn, and the magnetic stirring reaction was carried out at 30°C for 0.5h; a sample was taken every 5min, and the supernatant was taken out after each rest and analyzed by gas chromatography;
[0024] The content of DBT in the simulated fuel oil is confirmed by reference standards, analysis conditions:
[0025] Injection port temperature = 340°C; detector temperature = 250°C; furnace temperature = 70°C; carrier gas: high-purity nitrogen; injection volume: 1 μL.
[0026] 3. Catalyst recovery and recycling:
[0027] After the reaction is completed, th...
Embodiment 2
[0029] 1. Preparation of simulated fuel oil:
[0030] With embodiment 1.
[0031] 2. Catalytic oxidation desulfurization experiment:
[0032] 10.61mg Na 9 lmao 10 o 36 32H 2 O, 0.03mL 30wt%H 2 o 2, 1mL ionic liquid [BMIM]BF 4 , 5mL simulated fuel oil was added to a 50mL double-necked round-bottom flask in turn, and the magnetic stirring reaction was carried out at 30°C for 0.6h; a sample was taken every 5min, and the supernatant was taken out after each rest and analyzed by gas chromatography;
[0033] The content of DBT in the simulated fuel oil is confirmed by reference standards, analysis conditions:
[0034] Injection port temperature = 340°C; detector temperature = 250°C; furnace temperature = 70°C; carrier gas: high-purity nitrogen; injection volume: 1 μL.
[0035] 3. Catalyst recovery and recycling:
[0036] After the reaction is completed, the poured out supernatant oil phase clear liquid is the fuel oil after deep desulfurization; after the residual fuel oil...
PUM
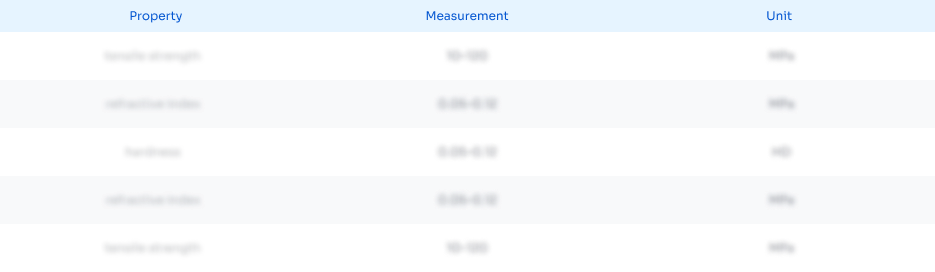
Abstract
Description
Claims
Application Information

- R&D
- Intellectual Property
- Life Sciences
- Materials
- Tech Scout
- Unparalleled Data Quality
- Higher Quality Content
- 60% Fewer Hallucinations
Browse by: Latest US Patents, China's latest patents, Technical Efficacy Thesaurus, Application Domain, Technology Topic, Popular Technical Reports.
© 2025 PatSnap. All rights reserved.Legal|Privacy policy|Modern Slavery Act Transparency Statement|Sitemap|About US| Contact US: help@patsnap.com