Near-net shape forming manufacturing method for thrust collars of sliding bearings of automobiles
The technology of a sliding bearing and a manufacturing method, which is applied in the field of near-net-shape manufacturing of a thrust ring of an automobile sliding bearing, can solve the problems of high manufacturing cost and large waste of materials, and achieves low manufacturing cost, high material utilization rate, and improved utilization rate. Effect
- Summary
- Abstract
- Description
- Claims
- Application Information
AI Technical Summary
Problems solved by technology
Method used
Image
Examples
Embodiment Construction
[0023] specific implementation plan
[0024] Such as Figure 1 to Figure 5 As shown, a near-net-shape manufacturing method of an automobile sliding bearing thrust ring is: use a seamless steel pipe as the steel backing of the sliding bearing thrust ring, and first press the thickness and thickness of the steel backing of the sliding bearing thrust ring Select a seamless steel pipe with the same wall thickness and inner hole diameter for the inner hole, then calculate the length of the seamless steel pipe according to the outer diameter of the sliding bearing thrust ring, and cut a section of the seamless steel pipe horizontally as the steel lining of the sliding bearing thrust ring Backing material.
[0025] Put the steel backing material 6 in the lower mold 7 of the axial rolling machine for rotary processing, the lower mold moves up and feeds during processing, and rotates with the upper mold 5 of the rotary rolling machine with an eccentric swing angle of 1.5°-5° When ent...
PUM
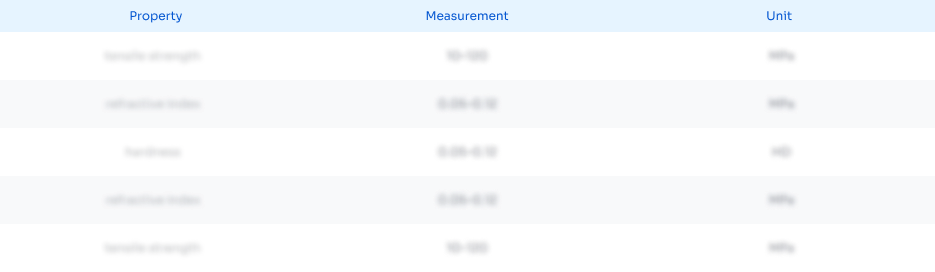
Abstract
Description
Claims
Application Information

- R&D
- Intellectual Property
- Life Sciences
- Materials
- Tech Scout
- Unparalleled Data Quality
- Higher Quality Content
- 60% Fewer Hallucinations
Browse by: Latest US Patents, China's latest patents, Technical Efficacy Thesaurus, Application Domain, Technology Topic, Popular Technical Reports.
© 2025 PatSnap. All rights reserved.Legal|Privacy policy|Modern Slavery Act Transparency Statement|Sitemap|About US| Contact US: help@patsnap.com