Method for brazing foamed aluminum plate and aluminum plate by removing interfacial oxide films through bubble wall friction
A foamed aluminum plate and oxide film technology, which is used in welding equipment, welding/welding/cutting items, manufacturing tools, etc., can solve the problems of low joint strength of foamed aluminum and aluminum plate, difficult to remove oxide film, and non-wetting of solder. Achieve improved wetting and spreading, short welding cycle times and low cost
- Summary
- Abstract
- Description
- Claims
- Application Information
AI Technical Summary
Problems solved by technology
Method used
Image
Examples
specific Embodiment approach 1
[0014] Specific implementation mode one: combine Figure 1 to Figure 5 Describe this implementation mode, this implementation mode is realized through the following steps:
[0015] Step 1, cleaning and drying the foamed aluminum plate 2 and the dense aluminum plate 3;
[0016] Step 2: Heat the aluminum foam board 2 as a whole to above the melting point of the brazing material, that is, between 350°C and 460°C, and use the rod-shaped Zn-Al-Cu brazing filler metal to reciprocate on the surface to be welded of the aluminum foam board 2, see figure 1 , so that the melted brazing material is evenly coated on the surface of the foamed aluminum plate 2 to be welded, see figure 2 , naturally cooled to room temperature (20 ° C ~ 25 ° C);
[0017] Step 3: Fix the weldment of the dense aluminum plate 3 on the fixing jig 6, fix the weldment of the foamed aluminum plate 2 coated with brazing material on the sliding jig 5, and coat the end surface of the foamed aluminum plate 2 with braz...
specific Embodiment approach 2
[0020] Embodiment 2: The heating temperature in step 1 of this embodiment is 400°C-430°C. Other steps are the same as in the first embodiment.
specific Embodiment approach 3
[0021] Embodiment 3: In step 2 of this embodiment, the way of heating the aluminum foam board 2 as a whole adopts a propane flame or an oxyacetylene flame. Other steps are the same as in the first embodiment.
PUM
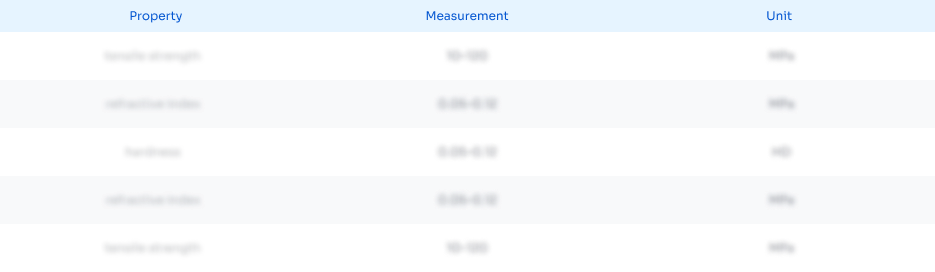
Abstract
Description
Claims
Application Information

- R&D
- Intellectual Property
- Life Sciences
- Materials
- Tech Scout
- Unparalleled Data Quality
- Higher Quality Content
- 60% Fewer Hallucinations
Browse by: Latest US Patents, China's latest patents, Technical Efficacy Thesaurus, Application Domain, Technology Topic, Popular Technical Reports.
© 2025 PatSnap. All rights reserved.Legal|Privacy policy|Modern Slavery Act Transparency Statement|Sitemap|About US| Contact US: help@patsnap.com