Casting method for glass mould blank
A glass mold and blank technology, used in casting molding equipment, casting molds, casting mold components, etc., can solve the problems of high casting cost, low hardness, damage to the nasal mucosa, etc., to ensure the quality of castings, improve casting efficiency, guarantee The effect of physical properties
- Summary
- Abstract
- Description
- Claims
- Application Information
AI Technical Summary
Problems solved by technology
Method used
Image
Examples
Embodiment 1
[0014] according to figure 1 Process flow shown.
[0015] First, according to the size requirements on the glass mold blank drawing provided by the user, the wood model base plate 1 with a pair of bottle molds 11, sprue mold 12, sprue mold 13 and filter screen mold 14 is processed by wooden mold workers; 2 Place the cover on the wooden model bottom plate 1, and fill the cavity of the mold frame 2 with coal powder sand 3; then turn the mold frame 2 filled with coal powder sand 3 together with the wooden model bottom plate 1 by 180°, and remove Wooden model base plate 1, obtains the mold that has a pair of bottle mold cavity 111, sprue 121, runner 131 and filter screen cavity 141, and the filter screen 1411 that material is pottery is inserted in the filter screen cavity 141; Then a The cold iron slime core 4 is placed on the bottle mold cavity 111; finally, the molten iron is poured from the gate 121, and the molten iron enters the bottle mold cavity 111 through the runne...
Embodiment 2
[0017] Only change the parts by weight of the quartz sand that constitutes the raw material of coal powder sand 3 to 98.5 parts, change the parts by weight of coal dust to 0.5 parts, and change the parts by weight of bentonite to 1 part, which has been proved by the applicant's experiment , if the weight part of coal powder is less than 0.5 part, then the molten iron will penetrate into the sand mold, which will affect the surface quality of the casting; similarly, if the weight part of bentonite is less than 1 part, it will affect the bonding strength and produce sand loss defects. The strength of the mold is poor. All the other are the same as the description to embodiment 1.
Embodiment 3
[0019] Change the parts by weight of quartz sand, bentonite (calcium-based bentonite instead) and coal powder to 98.8 parts, 1.3 parts and 0.7 parts respectively, and the rest are the same as those described in Example 1.
PUM
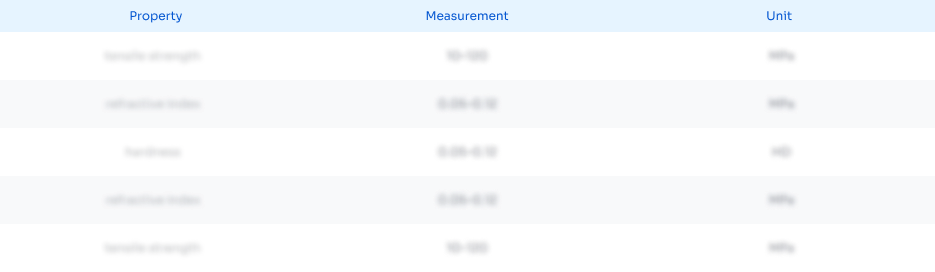
Abstract
Description
Claims
Application Information

- R&D Engineer
- R&D Manager
- IP Professional
- Industry Leading Data Capabilities
- Powerful AI technology
- Patent DNA Extraction
Browse by: Latest US Patents, China's latest patents, Technical Efficacy Thesaurus, Application Domain, Technology Topic, Popular Technical Reports.
© 2024 PatSnap. All rights reserved.Legal|Privacy policy|Modern Slavery Act Transparency Statement|Sitemap|About US| Contact US: help@patsnap.com