Radiating pipe base and machining method thereof
A manufacturing method and heat dissipation pipe technology, applied in the direction of tubular elements, heat exchange equipment, lighting and heating equipment, etc., can solve the problems of cost increase, affecting heat dissipation effect, and not meeting economic benefits, etc.
- Summary
- Abstract
- Description
- Claims
- Application Information
AI Technical Summary
Problems solved by technology
Method used
Image
Examples
Embodiment Construction
[0026] The present invention will be further described below in conjunction with the accompanying drawings and specific embodiments.
[0027] Such as Figure 1 to Figure 4 As shown, it is the first embodiment of the design of the heat dissipation pipe seat of the present invention, which is integrally formed into a hollow tubular hollow pipe body 1, and the hollow pipe body 1 is provided with an integral body at the front end (or middle position). Connected closed surfaces 11 (such as image 3 , Figure 4 ), and the tube wall is also integrally formed with a plurality of clamping grooves 12 for the surrounding combination of a plurality of heat dissipation fins 2, so that the plurality of heat dissipation fins 2 are tightly fitted and densely inserted into the heat dissipation tube base 1 The peripheral wall is used to form a heat dissipation pipe base 1 with heat dissipation fins 2 .
[0028] The present invention forms the hollow tube body 1, the closed surface 11 and the...
PUM
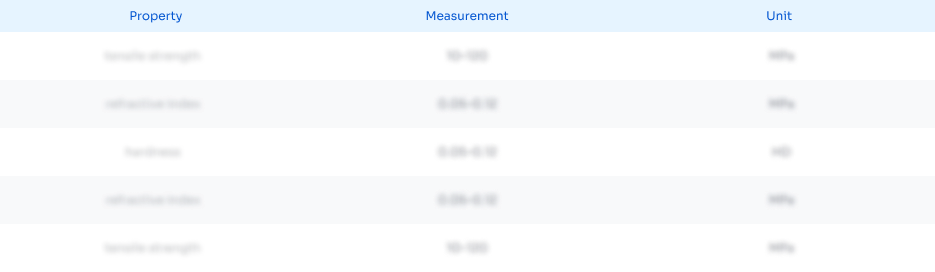
Abstract
Description
Claims
Application Information

- R&D
- Intellectual Property
- Life Sciences
- Materials
- Tech Scout
- Unparalleled Data Quality
- Higher Quality Content
- 60% Fewer Hallucinations
Browse by: Latest US Patents, China's latest patents, Technical Efficacy Thesaurus, Application Domain, Technology Topic, Popular Technical Reports.
© 2025 PatSnap. All rights reserved.Legal|Privacy policy|Modern Slavery Act Transparency Statement|Sitemap|About US| Contact US: help@patsnap.com