Mixed dry-distillation oil refining method for wrapping oil shales with small particles and blocky oil shales, and wrapping bags
A technology of oil shale and small particles, which is applied in the field of oil shale carbonization and refining, can solve the problems of affecting the heat conduction in the furnace, affecting the effect of carbonization, and poor thermal stability, so as to achieve effective use of resources, increase economic benefits, and good carbonization effect Effect
- Summary
- Abstract
- Description
- Claims
- Application Information
AI Technical Summary
Problems solved by technology
Method used
Image
Examples
Embodiment Construction
[0014] The mixed carbonization refining method of encapsulating small-particle oil shale and massive oil shale in the present invention does not change the gas heat carrier carbonization process or solid heat carrier rotary carbonization process familiar to those skilled in the art, but only in the oil shale batching process, Mix small-grained oil shale < 8 mm in several bags into the massive oil shale of 8-85 mm, the total weight of the small-grained oil shale < 8 mm packed in several bags It accounts for 20-30% of the total weight of retort oil shale.
[0015] The package bag structure of the present invention is as figure 1 As shown, the wrapping bag includes an open wrapping bag made of at least one fiber cloth of medium-alkali glass fiber cloth, non-alkali glass fiber cloth, asbestos fiber cloth, and ceramic fiber cloth. After the rock, the pocket is sewn closed. It can also be made of metal mesh. The package bag of this embodiment is Ф70×120㎜. Such as figure 2 As s...
PUM
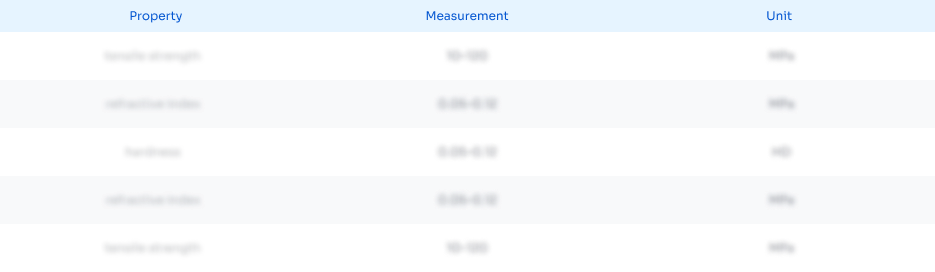
Abstract
Description
Claims
Application Information

- R&D Engineer
- R&D Manager
- IP Professional
- Industry Leading Data Capabilities
- Powerful AI technology
- Patent DNA Extraction
Browse by: Latest US Patents, China's latest patents, Technical Efficacy Thesaurus, Application Domain, Technology Topic, Popular Technical Reports.
© 2024 PatSnap. All rights reserved.Legal|Privacy policy|Modern Slavery Act Transparency Statement|Sitemap|About US| Contact US: help@patsnap.com