Method for preparing grinding wheel according to wet method
A grinding wheel, wet process technology, applied in manufacturing tools, metal processing equipment, grinding/polishing equipment, etc., can solve the problems of uneven distribution and size of pores, irregular formation of pores, cracks in products, etc. and porosity, size and distribution uniformity, uniformity and strength improvement
- Summary
- Abstract
- Description
- Claims
- Application Information
AI Technical Summary
Problems solved by technology
Method used
Examples
Embodiment 1
[0038] A method for wet preparation of emery wheels, comprising the following preparation steps:
[0039] Step A, calculated by weight percentage, put 30% powder glue, 10% rice starch, 1% urea-formaldehyde resin, 0.1% polyvinyl alcohol and water into the reactor and stir for 20 minutes to mix, the stirring speed is: 400 revs / min, obtain mixed substance I;
[0040] Step B, the mixed substance I obtained in step A was left to stand for 7 minutes;
[0041] Step C, adding silicon carbide into the reactor, the weight ratio of the mixed substance I to the silicon carbide in the reactor is 1.2:1; stirring for 20 minutes for mixing, the stirring speed is: 400 rpm, and the mixed substance II is obtained;
[0042] Step D, then add 3% curing agent (curing agent: oxalic acid) into the reactor, the volume percent concentration of the curing agent is 0.1%; stir for 10 minutes to mix, the stirring speed is: 300 rpm, to obtain the mixed Substance III;
[0043] Step E, pouring the mixed sub...
Embodiment 2
[0048] A method for wet preparation of emery wheels, comprising the following preparation steps:
[0049] Step A, calculated by weight percentage, put 35% powder glue, 15% potato starch, 2% urea-formaldehyde resin, 0.2% polyurethane resin and water in the reactor and stir for 25 minutes to mix, the stirring speed is: 450 revs / min, obtain mixed substance I;
[0050] Step B, the mixed substance I obtained in step A was left to stand for 8 minutes;
[0051] Step C, adding silicon carbide into the reactor, the weight ratio of the mixed substance I in the reactor to silicon carbide is 1.4:1; stirring for 25 minutes for mixing, the stirring speed is: 450 rpm, and the mixed substance II is obtained;
[0052] Step D, adding 4% acetic acid into the reactor, the volume percent concentration of the acetic acid is 0.3%; stirring for 18 minutes for mixing, the stirring speed is: 380 rpm, to obtain the mixed substance III;
[0053] Step E, pouring the mixed substance III obtained in step D,...
Embodiment 3
[0058] A method for wet preparation of emery wheels, comprising the following preparation steps:
[0059] Step A, calculated by weight percentage, with 42% powder glue, 10% starch (including 2% millet starch, 2% corn starch and 6% sweet potato starch), 3% urea-formaldehyde resin, 0.2% The polyvinyl acetal resin and water were placed in the reactor and stirred for 32 minutes to mix, the stirring speed was: 500 rpm, and the mixed substance I was obtained;
[0060] Step B, the mixed substance I obtained in step A was left to stand for 8 minutes;
[0061] Step C, adding silicon carbide into the reactor, the weight ratio of the mixed substance I in the reactor to silicon carbide is 1.6:1; stirring for 30 minutes for mixing, the stirring speed is: 550 rpm, and the mixed substance II is obtained;
[0062] Step D, add 5% curing agent (wherein, comprise 2% malic acid and 3% citrate) in reactor again, the volume percentage concentration of described curing agent is 0.2%; Stir 12 minute...
PUM
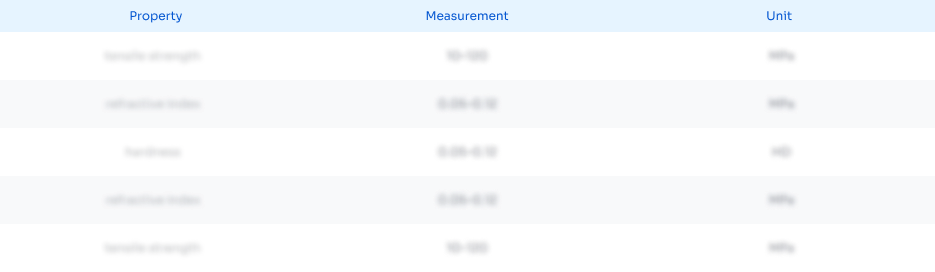
Abstract
Description
Claims
Application Information

- R&D
- Intellectual Property
- Life Sciences
- Materials
- Tech Scout
- Unparalleled Data Quality
- Higher Quality Content
- 60% Fewer Hallucinations
Browse by: Latest US Patents, China's latest patents, Technical Efficacy Thesaurus, Application Domain, Technology Topic, Popular Technical Reports.
© 2025 PatSnap. All rights reserved.Legal|Privacy policy|Modern Slavery Act Transparency Statement|Sitemap|About US| Contact US: help@patsnap.com