Diamond grinding block dressing device for polished tile
A dressing device and diamond technology, applied in the direction of abrasive surface adjustment device, grinding/polishing equipment, grinding workpiece support, etc., can solve the problems of low dressing efficiency, poor straightness of grinding block, etc., achieve uniform dressing, simple control, The effect of easy operation
- Summary
- Abstract
- Description
- Claims
- Application Information
AI Technical Summary
Problems solved by technology
Method used
Image
Examples
specific Embodiment approach 1
[0013] Specific implementation mode one: as Figure 1~3 As shown, the diamond grinding block dressing device for polishing tiles of the present embodiment includes a first large pulley 1, a first small pulley 2, a first screw guide workbench 3, a first insulating plate 4, a first transmission shaft 6, a machine Frame 9, first grinding block fixture 11, first frequency conversion motor 12, first synchronous belt 14, first electrode 15, second drive shaft 16, second electrode 17, second synchronous belt 18, second frequency conversion motor 20, The second grinding block fixture 22, the second insulating plate 25, the second lead screw guide rail workbench 26, the second small pulley 27, the second large pulley 28 and four bearing blocks 10; the first lead screw guide rail workbench 3 The first screw guide rail workbench 26 is fixed on the upper end face of the frame 9 through the second insulating plate 25, and the first screw guide rail works The guide rail of table 3 and the ...
specific Embodiment approach 2
[0016] Embodiment 2: The groove 23 in this embodiment is a wedge-shaped groove. Such a design makes it easy to install diamond grinding blocks. Other components and connections are the same as those in the first embodiment.
[0017] working principle:
[0018] Such as Figure 1~3 As shown, multiple diamond grinding blocks are clamped on the first grinding block holder 11 and the second grinding block holder 22, and the first variable frequency motor 12 and the second variable frequency motor 20 are driven to rotate. The first variable frequency motor 12 and the second variable frequency motor The rotation of the motor 20 can be selected in the same direction or in the opposite direction. The first grinding block holder 11 and the second grinding block holder 22 are aligned, and then the first electrode 15 and the second electrode 17 are energized to make the first grinding block The diamond grinding blocks on the block holder 11 and the second grinding block holder 22 are c...
PUM
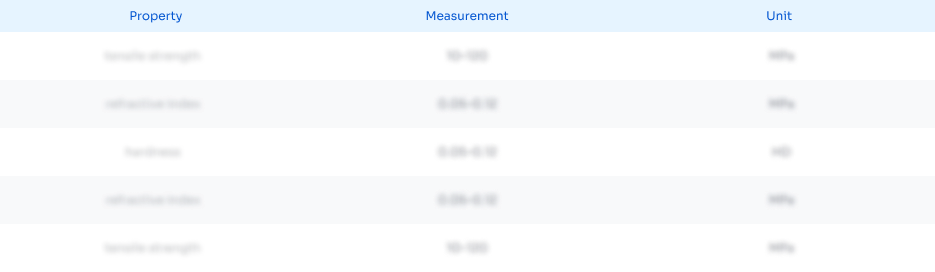
Abstract
Description
Claims
Application Information

- R&D
- Intellectual Property
- Life Sciences
- Materials
- Tech Scout
- Unparalleled Data Quality
- Higher Quality Content
- 60% Fewer Hallucinations
Browse by: Latest US Patents, China's latest patents, Technical Efficacy Thesaurus, Application Domain, Technology Topic, Popular Technical Reports.
© 2025 PatSnap. All rights reserved.Legal|Privacy policy|Modern Slavery Act Transparency Statement|Sitemap|About US| Contact US: help@patsnap.com