Method and tool for reducing deformation in large-scale thin-wall cylindrical forging heat treatment
A heat treatment process, thin-walled cylinder technology, applied in heat treatment furnaces, heat treatment equipment, furnace types, etc., can solve problems such as uneven support of forgings, and achieve the effects of facilitating processing, increasing contact area, and improving uneven support
- Summary
- Abstract
- Description
- Claims
- Application Information
AI Technical Summary
Problems solved by technology
Method used
Image
Examples
Embodiment Construction
[0019] The method for reducing deformation during heat treatment of large thin-walled cylinder forgings of the present invention comprises the following steps:
[0020] In the first step, the well-shaped parallel iron 1 is laid in the heat treatment furnace 3, and the well-shaped parallel iron 1 is used as a supporting tool;
[0021] The second step is to adjust the levelness of the well-shaped horn 1 so that the well-shaped horn 1 is in a horizontal state;
[0022] In the third step, the large thin-walled cylinder forging 2 is vertically placed on the well-shaped horn 1, and the line passing through the center of the well-shaped horn 1 and perpendicular to the horizontal plane of the well-shaped horn 1 coincides with the axis of the forging, as figure 1 shown.
[0023] In the first step, the well-shaped horn 1 is hoisted by a crane and placed in the heat treatment furnace 3. Since the well-shaped horn 1 is a tool for supporting the forging, its size is larger than that of th...
PUM
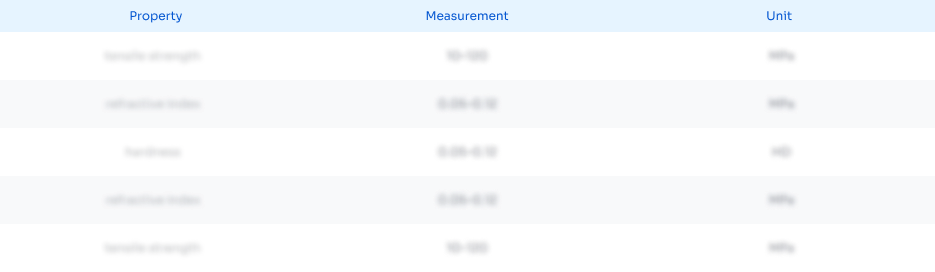
Abstract
Description
Claims
Application Information

- R&D Engineer
- R&D Manager
- IP Professional
- Industry Leading Data Capabilities
- Powerful AI technology
- Patent DNA Extraction
Browse by: Latest US Patents, China's latest patents, Technical Efficacy Thesaurus, Application Domain, Technology Topic, Popular Technical Reports.
© 2024 PatSnap. All rights reserved.Legal|Privacy policy|Modern Slavery Act Transparency Statement|Sitemap|About US| Contact US: help@patsnap.com