Nitrile rubber production process
A production process and technology of nitrile rubber, applied in the field of nitrile rubber production process, can solve the problems of fluctuation of initiator addition, degassing tower flushing, increase of vulcanization time, etc. Large, blending effect improved effect
- Summary
- Abstract
- Description
- Claims
- Application Information
AI Technical Summary
Problems solved by technology
Method used
Image
Examples
Embodiment 1
[0040] 1. Polymerization
[0041] The raw materials acrylonitrile 1, butadiene 2, desalted deoxygenated water 3, concentrated water phase 4 and molecular weight regulator 5 (TDM, tert-dodecylmercaptan) are transported into the polymerization station together, and converge at the header 6 of the polymerization station. The mixed material after confluence passes through the pipeline pump 7 and the pipeline mixer 8 for material mixing (it also has a pre-emulsification effect when the material is mixed), and is cooled by heat exchange through the ammonia-cooled heat exchanger 9, and the cooled mixed material is mixed with the initiator emulsion 10 Together with the activator solution 11, it enters nine reactors 13 for polymerization to generate latex. The latex output from the fourth reactor enters the fifth reactor together with the molecular weight regulator emulsion 27. After the polymerization conversion rate reaches 70% ± 5, the ninth The latex coming out of the reaction kett...
Embodiment 2
[0052] 1. Polymerization
[0053] The raw materials acrylonitrile 1, butadiene 2, desalted deoxygenated water 3, concentrated water phase 4 and molecular weight regulator 5 (TDM, tert-dodecylmercaptan) are transported into the polymerization station together, and converge at the header 6 of the polymerization station. The mixed material after confluence passes through the pipeline pump 7 and the pipeline mixer 8 for material mixing in turn, and is cooled by heat exchange through the ammonia cooling heat exchanger 9, and the cooled mixed material, together with the initiator emulsion 10 and the activator solution 11, enters nine Reactor 13 polymerizes to generate latex, and the latex output from the fourth reactor enters the fifth reactor together with the molecular weight regulator emulsion 27. After the polymerization conversion rate reaches 70% ± 5, the latex that comes out of the ninth reactor 13 and terminates the defoaming The agent solution 12 enters the ripening kettle ...
Embodiment 3
[0064] 1. Polymerization
[0065] The raw materials acrylonitrile 1, butadiene 2, desalted deoxygenated water 3, concentrated water phase 4 and molecular weight regulator 5 (TDM, tert-dodecylmercaptan) are transported into the polymerization station together, and converge at the header 6 of the polymerization station. The mixed material after confluence passes through the pipeline pump 7 and the pipeline mixer 8 for material mixing in turn, and is cooled by heat exchange through the ammonia cooling heat exchanger 9, and the cooled mixed material, together with the initiator emulsion 10 and the activator solution 11, enters nine Reactor 13 polymerizes to generate latex, and the latex output from the fourth reactor enters the fifth reactor together with the molecular weight regulator emulsion 27. After the polymerization conversion rate reaches 70% ± 5, the latex that comes out of the ninth reactor 13 and terminates the defoaming The agent solution 12 enters the ripening kettle ...
PUM
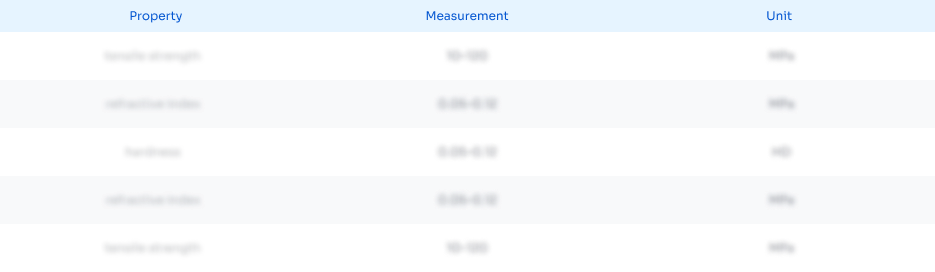
Abstract
Description
Claims
Application Information

- Generate Ideas
- Intellectual Property
- Life Sciences
- Materials
- Tech Scout
- Unparalleled Data Quality
- Higher Quality Content
- 60% Fewer Hallucinations
Browse by: Latest US Patents, China's latest patents, Technical Efficacy Thesaurus, Application Domain, Technology Topic, Popular Technical Reports.
© 2025 PatSnap. All rights reserved.Legal|Privacy policy|Modern Slavery Act Transparency Statement|Sitemap|About US| Contact US: help@patsnap.com