Method for preparing olefin by dehydrogenating low-carbon alkane
A technology for alkane dehydrogenation and olefin production, which is applied in the field of hydrocarbon dehydrogenation to olefin production, can solve the problems of high cracking temperature, complex components of cracked products, large process energy consumption, etc., and achieves the effect of improving conversion rate and selectivity
- Summary
- Abstract
- Description
- Claims
- Application Information
AI Technical Summary
Problems solved by technology
Method used
Image
Examples
Embodiment 1
[0040] The raw material nature and source used in the embodiment are listed in Table 1
[0041]
[0042] Catalyst preparation
[0043] 3%Cr / SiO 2 Catalyst preparation
[0044] 0.71 g of Cr(NO 3 ) 3 9H 2 O is dissolved in 2.25 milliliters of water, adding 3 grams of specific surface area is 640m 2 / g of silica impregnated, stirred evenly and placed at room temperature for 24 hours, then dried at 120°C for 2 hours.
[0045] In a static muffle furnace, dry silica loaded with chromium nitrate precursor was calcined in air at 600 °C for 4 hours to obtain 3% Cr / SiO 2 catalyst.
[0046] 3%Cr / SiO 2 -1 Preparation of catalyst
[0047] 0.71 g of Cr(NO 3 ) 3 9H 2 O was dissolved by adding 2.25 ml of water, impregnated by adding 3 g of silicon dioxide, stirred evenly and left at room temperature for 24 hours, then dried at 120°C for 2 hours.
[0048] In a static muffle furnace, the dried silicon dioxide loaded with chromium nitrate precursor was roasted in air in multi-sta...
Embodiment 2
[0068] Load 0.3g catalyst in stainless steel reactor (inner diameter 6mm), catalyst is in N 2 Raise the temperature to 600°C under purging, and then switch to the reaction gas, whose specific composition is 20%C 3 h 8 , 80% CO or CO 2 or N 2 , the above percentages are mole percentages, and the space velocity of the feed stream is 1750h -1 , The reacted product enters the chromatogram for analysis, and after reacting for 6 minutes under normal pressure, record the fresh yield of propylene. The results of the analysis are listed in Table 2.
[0069] Table 2C 3 h 8 Respectively and CO, CO 2 , N 2 Reaction results on catalysts with different Cr loadings
[0070]
[0071] It can be seen from Table 2 that propane reacts in different gas atmospheres, and the promotion effect of carbon monoxide on propane dehydrogenation reaction is greater than that of carbon dioxide and nitrogen; Propylene selectivity.
Embodiment 3
[0072] Example 3 The reaction results of multi-stage heating and roasting catalyst in air atmosphere
[0073] In addition to changing the catalyst to 3% Cr / SiO 2 -1 catalyst, carry out propane dehydrogenation reaction in the same manner as in Example 2. The results are shown in Table 3.
[0074] Table 3C 3 h 8 Respectively and CO, CO 2 , N 2 In Catalyst 3%Cr / SiO 2 The result of the reaction on -1
[0075]
[0076] From the comparison of Table 3 and Table 2, it can be seen that the catalyst prepared by multi-stage heating is better than the catalyst in Example 1 in terms of propane conversion and propylene selectivity.
PUM
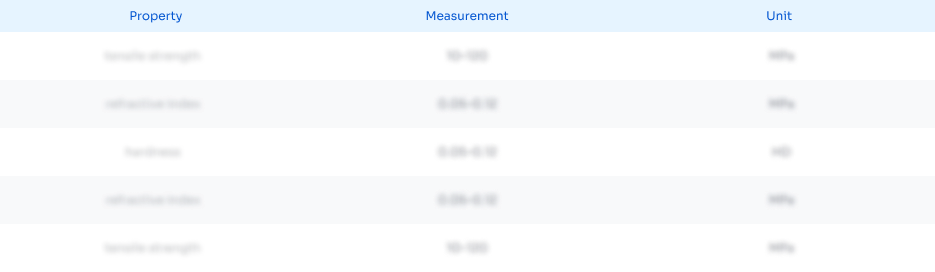
Abstract
Description
Claims
Application Information

- R&D Engineer
- R&D Manager
- IP Professional
- Industry Leading Data Capabilities
- Powerful AI technology
- Patent DNA Extraction
Browse by: Latest US Patents, China's latest patents, Technical Efficacy Thesaurus, Application Domain, Technology Topic, Popular Technical Reports.
© 2024 PatSnap. All rights reserved.Legal|Privacy policy|Modern Slavery Act Transparency Statement|Sitemap|About US| Contact US: help@patsnap.com