e/LQFP (low-profile quad flat package) planar packaging part with grounded ring and production method of e/LQFP planar packaging part with grounded ring
A production method and a grounding ring technology, which are applied in semiconductor/solid-state device manufacturing, semiconductor/solid-state device components, electrical components, etc., can solve the problem of large chip bonding, non-stick carrier silver plating area, easy-to-scan separation layer, etc. problem, to achieve the effect of increasing bonding force, high reliability and test yield, and improving reliability and test yield
- Summary
- Abstract
- Description
- Claims
- Application Information
AI Technical Summary
Problems solved by technology
Method used
Image
Examples
Embodiment 1
[0088] The wafer is thinned by the existing process method to obtain a thinned wafer with a final thinned thickness of 150 μm; during the thinning process, the rough grinding speed is 5 μm / s, and the thickness of the wafer after rough grinding is 200 μm + film thickness; The fine grinding speed is 0.5μm / s, and the thickness of the wafer after fine grinding is 150μm+the thickness of the film, and the process of preventing chip warpage is adopted when thinning; the DISC 3350 dicing machine is used for scribing; when scribing, the scribing feed is controlled. Speed ≤ 10mm / s, and adopts anti-fragmentation, anti-crack scribing process software control technology; use conductive adhesive to paste IC chips, fix IC chips on the die bonding machine, send the lead frame with grounding ring to the feeding table, and paste the chips The machine grabs a lead frame and sends it into the track, and after sending it to the chip bonding table, apply conductive glue on the carrier 1. The condu...
Embodiment 2
[0090] The wafer is thinned by the existing process method to obtain a thinned wafer with a final thinning thickness of 200 μm; during the thinning process, the rough grinding speed is 3 μm / s, and the thickness of the wafer after rough grinding is 250 μm + film thickness The fine grinding speed is 0.8μm / s, and the thickness of the wafer after fine grinding is 200μm+the thickness of the film, and the process of preventing chip warpage is adopted when reducing the thickness; the double-knife dicing machine is used for scribing; Knife speed ≤ 10mm / s, and adopts anti-fragmentation, anti-crack scribing process software control technology; use insulating glue to paste IC chips, fix IC chips on the chip bonding machine, send the lead frame with grounding ring to the feeding table, stick The chip machine grabs a lead frame and sends it into the track, and after sending it to the bonding table, apply insulating glue on the carrier 1. The insulating glue is the first bonding material 10,...
Embodiment 3
[0092] The wafer is thinned by the existing process method to obtain a thinned wafer with a final thinning thickness of 175 μm; during the thinning process, the rough grinding speed is 4 μm / s, and the thickness of the wafer after rough grinding is 225 μm + film thickness ;Finish grinding speed is 0.5μm / s, the thickness of the wafer after fine grinding is 175μm+film thickness, the process of preventing chip warping is adopted when thinning; A-WD-300TXB dicing machine is used for scribing; when scribing, control Scribing feed speed ≤10mm / s, and adopts anti-fragmentation and anti-crack scribing process software control technology; uses adhesive film to paste IC chip, and puts the IC chip with adhesive film directly through the adhesive film chip loading machine On the carrier 1, the IC chip is bonded to the carrier 1, and the IC chip is the first IC chip 11, and a lead frame is glued and delivered to the receiving box; after bonding all the first IC chips 11 of this batch in the s...
PUM
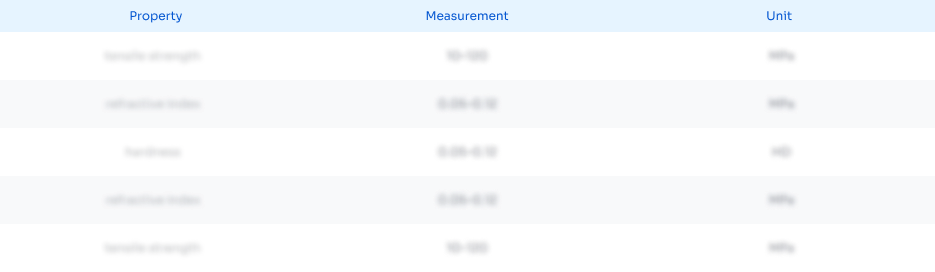
Abstract
Description
Claims
Application Information

- Generate Ideas
- Intellectual Property
- Life Sciences
- Materials
- Tech Scout
- Unparalleled Data Quality
- Higher Quality Content
- 60% Fewer Hallucinations
Browse by: Latest US Patents, China's latest patents, Technical Efficacy Thesaurus, Application Domain, Technology Topic, Popular Technical Reports.
© 2025 PatSnap. All rights reserved.Legal|Privacy policy|Modern Slavery Act Transparency Statement|Sitemap|About US| Contact US: help@patsnap.com