Production process of highly wear-resistant polyester-viscose fabrics
A production process and fabric technology, applied in fabric surface trimming, weaving, yarn and other directions, can solve the problems that polyester-viscose fabrics cannot be fully satisfied, the finished product width is different, and there is no drape feeling, etc., to achieve standard hollow effect and color difference Small, good moisture wicking and breathability effect
- Summary
- Abstract
- Description
- Claims
- Application Information
AI Technical Summary
Problems solved by technology
Method used
Examples
Embodiment 1
[0036] (1) Raw material yarn treatment: 20S / 1 polyester viscose yarn and 14S / 1 polyester viscose yarn are used as raw material yarns, and the two raw material yarns are subjected to high-temperature steaming and shaping. The setting temperature is 100°C and the setting time is uniform 110min;
[0037] (2) Balance re-humidity: place the two kinds of raw material yarns in the warehouse for more than 30 days in a balanced re-humidity state;
[0038] (3) Winding: winding the two raw material yarns respectively;
[0039] (4) Network coating: 14S / 1 polyester viscose yarn is mechanically coated with 40D spandex through a staple fiber spandex coating machine, and the speed of the staple fiber spandex coating machine is 600 rpm;
[0040] (5) Two-for-one twisting: 20S / 1 polyester viscose yarn, 14S / 1 polyester viscose yarn and 14S / 1 polyester viscose + 40D spandex yarn are twisted on the two-for-one twister according to the twist of 1850 twists / m to obtain 20S / 1 1 polyester viscose str...
Embodiment 2
[0048] (1) Raw material yarn treatment: 20S / 1 polyester viscose yarn and 14S / 1 polyester viscose yarn are used as raw material yarns, and the two raw material yarns are subjected to high-temperature steaming and setting. The setting temperature is 105°C and the setting time is uniform. 110min;
[0049] (2) Balance re-humidity: place the two kinds of raw material yarns in the warehouse for more than 30 days in a balanced re-humidity state;
[0050](3) Winding: winding the two raw material yarns respectively;
[0051] (4) Network coating: 14S / 1 polyester viscose yarn is mechanically coated with 40D spandex through a staple fiber spandex coating machine, and the speed of the staple fiber spandex coating machine is 700 rpm;
[0052] (5) Two-for-one twisting: 20S / 1 polyester viscose yarn, 14S / 1 polyester viscose yarn and 14S / 1 polyester viscose + 40D spandex yarn are twisted on the two-for-one twister according to the twist of 1800 twists / m to obtain 20S / 1 1 polyester viscose str...
Embodiment 3
[0060] (1) Raw material yarn treatment: 20S / 1 polyester viscose yarn and 14S / 1 polyester viscose yarn are used as raw material yarns, and the two raw material yarns are subjected to high-temperature steaming and setting. The setting temperature is 105°C and the setting time is uniform. 120min;
[0061] (2) Balance re-humidity: place the two kinds of raw material yarns in the warehouse for more than 30 days in a balanced re-humidity state;
[0062] (3) Winding: winding the two raw material yarns respectively;
[0063] (4) Network coating: 14S / 1 polyester viscose yarn is mechanically coated with 40D spandex through a staple fiber spandex coating machine, and the speed of the staple fiber spandex coating machine is 800 rpm;
[0064] (5) Two-for-one twisting: 20S / 1 polyester viscose yarn, 14S / 1 polyester viscose yarn and 14S / 1 polyester viscose + 40D spandex yarn are twisted on the two-for-one twister according to the twist of 1800 twists / m to obtain 20S / 1 1 polyester viscose st...
PUM
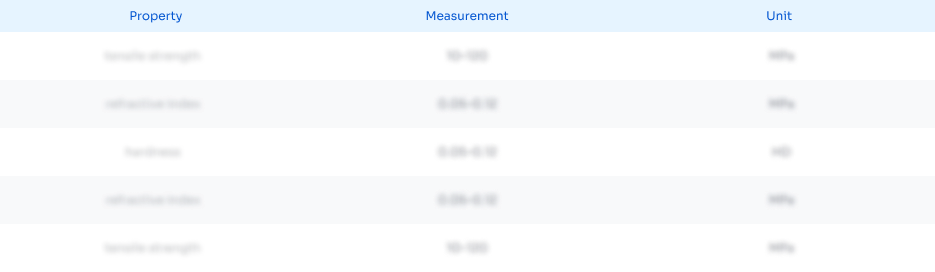
Abstract
Description
Claims
Application Information

- R&D Engineer
- R&D Manager
- IP Professional
- Industry Leading Data Capabilities
- Powerful AI technology
- Patent DNA Extraction
Browse by: Latest US Patents, China's latest patents, Technical Efficacy Thesaurus, Application Domain, Technology Topic, Popular Technical Reports.
© 2024 PatSnap. All rights reserved.Legal|Privacy policy|Modern Slavery Act Transparency Statement|Sitemap|About US| Contact US: help@patsnap.com