Preparation method of novel Mannich water-based epoxy curing agent
A water-based epoxy and curing agent technology, used in epoxy resin coatings, coatings, etc., can solve the problems of short pot life, low coating film hardness and high water absorption of water-based epoxy systems, and achieve long pot life and coating film. High hardness, low volatility effect
- Summary
- Abstract
- Description
- Claims
- Application Information
AI Technical Summary
Problems solved by technology
Method used
Image
Examples
Embodiment 1
[0019] Step 1: Mix 26.5g of 2,4,6-tris(dimethylaminomethyl)phenol with 64g of polyetheramine, stir and heat up to 70°C, and react for 8h to obtain Mannich modified amine A1.
[0020] The second step: under nitrogen blanketing conditions, put 60g polyethylene glycol 6000 and 3.8g E-51 into a four-necked flask equipped with a reflux condenser, a thermometer and a mechanical stirring device, stir, heat up, and heat the reactants When the temperature reaches about 60°C, the catalyst boron trifluoride diethyl ether is added, and the temperature is raised to 80°C, and the constant temperature reaction is maintained for 4 hours to obtain the terminal functional group epoxy prepolymer P.
[0021] Step 3: Add 2.5g of P and 15.5g of A1 into a three-necked flask, raise the temperature to 70°C, add 3.8g of E-51 into the reaction flask, and maintain a constant temperature for 3 hours. Then 4.5 g of phenyl glycidyl ether was added, and the temperature was raised to 80° C. for 2 h. The modi...
Embodiment 2
[0023] Step 1: Mix 26.5g of 2,4,6-tris(dimethylaminomethyl)phenol with 31g of diethylenetriamine, stir and heat up to 70°C, and react for 8h to obtain Mannich modified amine A1.
[0024] The second step: under nitrogen blanketing conditions, put 60g polyethylene glycol 6000 and 3.8g E-51 into a four-necked flask equipped with a reflux condenser, a thermometer and a mechanical stirring device, stir, heat up, and heat the reactants When the temperature reaches about 60°C, a catalyst, triphenylphosphine, is added, and the temperature is raised to 80°C, and the reaction is maintained at a constant temperature for 4 hours to obtain the terminal functional group epoxy prepolymer P.
[0025] Step 3: Add 5.5g of P and 15.5g of A1 into a three-necked flask, raise the temperature to 70°C, add 34g of E-51 into the reaction flask, and maintain a constant temperature for 3h. The modified Mannich amine A2 was obtained, the temperature was lowered, and the modified product A2 was emulsified ...
Embodiment 3
[0027] Step 1: Mix 26.5g of 2,4,6-tris(dimethylaminomethyl)phenol with 31g of diethylenetriamine, stir and heat up to 70°C, and react for 8h to obtain Mannich modified amine A1.
[0028] Step 2: Add 15.5g of A1 into a three-necked flask, raise the temperature to 70°C, add 2.85g of E-51 into the reaction flask, and maintain a constant temperature for 3h. The modified Mannich amine A2 was obtained, the temperature was lowered, and the modified product A2 was emulsified when the temperature was lowered to 50° C. to obtain the nonionic water-based epoxy curing agent emulsion M3.
PUM
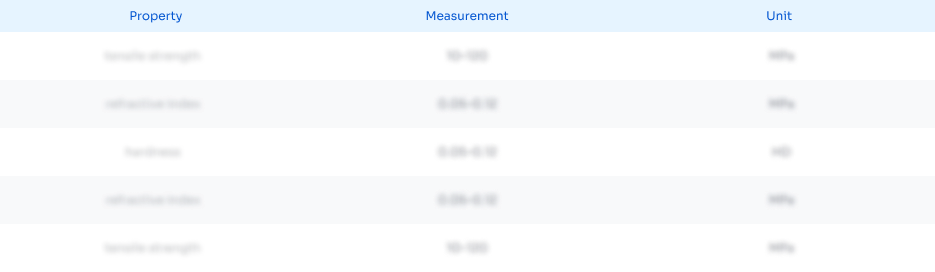
Abstract
Description
Claims
Application Information

- Generate Ideas
- Intellectual Property
- Life Sciences
- Materials
- Tech Scout
- Unparalleled Data Quality
- Higher Quality Content
- 60% Fewer Hallucinations
Browse by: Latest US Patents, China's latest patents, Technical Efficacy Thesaurus, Application Domain, Technology Topic, Popular Technical Reports.
© 2025 PatSnap. All rights reserved.Legal|Privacy policy|Modern Slavery Act Transparency Statement|Sitemap|About US| Contact US: help@patsnap.com