Method for producing tetrafluoroethylene by monochlorodifluoromethane thermal pyrolysis process
A technology of difluoromonochloromethane and tetrafluoroethylene, applied in chemical instruments and methods, halogenated hydrocarbon preparation, organic chemistry, etc., to achieve the effect of making good use of cold and heat, stable quality and reasonable process
- Summary
- Abstract
- Description
- Claims
- Application Information
AI Technical Summary
Problems solved by technology
Method used
Image
Examples
Embodiment 1
[0019] A method for producing tetrafluoroethylene by pyrolysis of difluorochloromethane;
[0020] Quantitatively send 1,000 kg / hour of difluorochloromethane into the high-nickel alloy cracking reactor continuously for cracking. The cracking reactor is a tubular furnace structure and can be heated by liquefied gas. The temperature of the cracking reactor is controlled at 800°C, and the pressure Lower than 0.15Mpa; the pyrolysis gas from the pyrolysis reactor is recovered by the preheating boiler, quenched by the quencher and then enters the hydrogen chloride absorber, then add 950 liters / hour water washing and 950 liters / hour alkali washing into the gas cabinet, and then freeze Dehydration, drying, compression and collection into the crude product tank, through multi-tower rectification, removal of light components and part of high boilers, recovery of unreacted HCFC-22, together with part of high boilers returned to the cracking reactor; separation of tetrafluoroethylene V...
Embodiment 2
[0022] The method for producing tetrafluoroethylene by pyrolysis of difluorochloromethane:
[0023] The quantitative 1000-1200 kg / hour of difluorochloromethane is continuously sent to the high-nickel alloy cracking reactor for cracking. The cracking reactor is a tube furnace structure and can be heated by liquefied gas. The temperature of the cracking reactor is controlled at 900 °C , the pressure is lower than 0.15Mpa; the pyrolysis gas from the cracking reactor is recovered by the preheating boiler, and after being quenched by the quencher, it enters the hydrogen chloride absorber, and then adds 1100 liters / hour of water washing and 1100 liters / hour of alkali washing into the gas cabinet, and then After freeze-dehydration, drying, and compression, it is collected into the crude product tank, and through multi-column rectification, light components and part of high boilers are removed, unreacted HCFC-22 is recovered, and part of high boilers are returned to the cracking re...
PUM
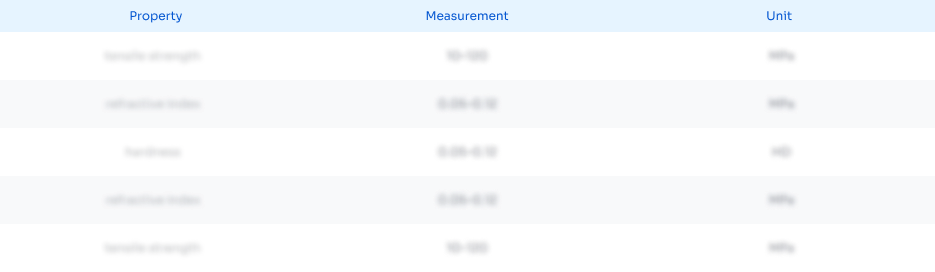
Abstract
Description
Claims
Application Information

- R&D
- Intellectual Property
- Life Sciences
- Materials
- Tech Scout
- Unparalleled Data Quality
- Higher Quality Content
- 60% Fewer Hallucinations
Browse by: Latest US Patents, China's latest patents, Technical Efficacy Thesaurus, Application Domain, Technology Topic, Popular Technical Reports.
© 2025 PatSnap. All rights reserved.Legal|Privacy policy|Modern Slavery Act Transparency Statement|Sitemap|About US| Contact US: help@patsnap.com