Processing method of wastes produced when battery grade lithium fluoride is manufactured by adopting carbonization method
A processing method and technology of lithium fluoride, applied in the directions of alkali metal fluoride, lithium carbonate;/acid carbonate, etc., can solve the problems of increasing the environmental protection pressure and production cost of battery-grade lithium fluoride.
- Summary
- Abstract
- Description
- Claims
- Application Information
AI Technical Summary
Problems solved by technology
Method used
Image
Examples
Embodiment 1
[0014] For the treatment method of the waste produced by the carbonization method of battery-grade lithium fluoride in this embodiment, refer to the process flow figure 1 , the specific steps are as follows:
[0015] A: 10 liters of lithium fluoride waste liquid produced in the production process of battery-grade lithium fluoride by carbonization method, 28 grams of sodium carbonate is added to the lithium fluoride waste liquid to react, and the added sodium carbonate and lithium fluoride in the solution react at 25 ℃ reaction, see reaction formula (1)
[0016] 2LiF+Na 2 CO 3 = Li 2 CO 3 ↓+2NaF (1)
[0017] After the reaction, the sodium carbonate that exceeded the reaction amount was dissolved in the solution, lithium carbonate formed a precipitate in the solution, filtered to obtain 35 grams of lithium carbonate ointment, and this lithium carbonate ointment can be directly returned to the carbonization method to prepare battery-grade lithium fluoride as a carbonization ...
Embodiment 2
[0026] For the treatment method of the waste produced by the carbonization method of battery-grade lithium fluoride in this embodiment, refer to the process flow figure 1 , the specific steps are as follows:
[0027] A: 20 liters of lithium fluoride waste liquid produced in the production process of battery-grade lithium fluoride by carbonization method, 61 grams of excess sodium carbonate (10% more than the reaction amount) was added to the lithium fluoride waste liquid to react, and the added sodium carbonate React with lithium fluoride in solution at 10°C, see reaction formula (1)
[0028] 2LiF+Na 2 CO 3 = Li 2 CO 3 ↓+2NaF (1)
[0029] After the reaction, the sodium carbonate that exceeded the reaction amount was dissolved in the solution, lithium carbonate formed a precipitate in the solution, filtered to obtain 65 grams of lithium carbonate ointment, and this lithium carbonate ointment can be directly returned to the carbonization method to prepare battery-grade lith...
Embodiment 3
[0038] For the treatment method of the waste produced by the carbonization method of battery-grade lithium fluoride in this embodiment, refer to the process flow figure 1 , the specific steps are as follows:
[0039] A: 30 liters of lithium fluoride waste liquid produced in the production process of battery-grade lithium fluoride by carbonization method, 88 grams of excess sodium carbonate (more than 5% of the reaction amount) was added to the lithium fluoride waste liquid to react, and the added carbonic acid Sodium reacts with lithium fluoride in the solution at 40°C, see reaction formula (1)
[0040] 2LiF+Na 2 CO 3 = Li 2 CO 3 ↓+2NaF (1)
[0041] After the reaction, the sodium carbonate that exceeded the reaction amount was dissolved in the solution, lithium carbonate formed a precipitate in the solution, filtered to obtain 95 grams of lithium carbonate ointment, and this lithium carbonate ointment can be directly returned to the carbonization method to prepare battery-g...
PUM
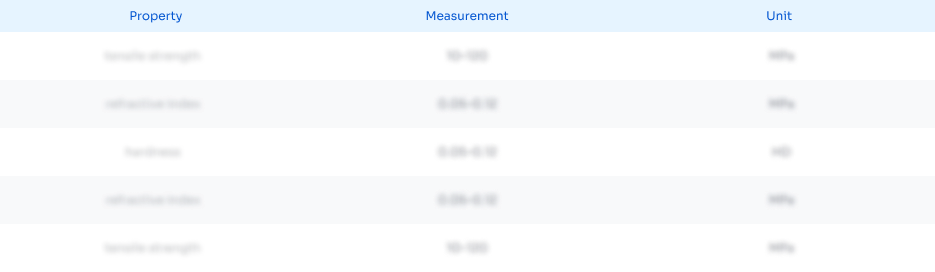
Abstract
Description
Claims
Application Information

- R&D Engineer
- R&D Manager
- IP Professional
- Industry Leading Data Capabilities
- Powerful AI technology
- Patent DNA Extraction
Browse by: Latest US Patents, China's latest patents, Technical Efficacy Thesaurus, Application Domain, Technology Topic, Popular Technical Reports.
© 2024 PatSnap. All rights reserved.Legal|Privacy policy|Modern Slavery Act Transparency Statement|Sitemap|About US| Contact US: help@patsnap.com