Method for preparing sodium sulfide from hydrogen sulfide waste gas produced in production of viscose fibre
A technology of viscose fiber and hydrogen sulfide, applied in the direction of alkali metal sulfide/polysulfide, etc., can solve the problems of low product quality, high iron ion content, short life of production equipment, etc., and achieve high product purity, high purity, The effect of fewer types of impurities
- Summary
- Abstract
- Description
- Claims
- Application Information
AI Technical Summary
Problems solved by technology
Method used
Image
Examples
Embodiment 1
[0057] The technical principle involved in the present invention is to use the principle of acid-base neutralization to absorb hydrogen sulfide waste gas with lye, and then use the principle of evaporation, concentration and crystallization to make the absorption liquid into sodium sulfide. The principle of the chemical equation is as follows:
[0058] 2NaOH+H 2 S=Na 2 S+2H 2 o
[0059] From the recovery of hydrogen sulfide waste gas to the production of sodium sulfide or sodium hydrosulfide, the overall process is as followsfigure 1 As shown, when the absorption liquid is evaporatively cooled and crystallized, the process steps are implemented figure 2 shown.
[0060] Below is a further description of the present invention, and the concrete steps are:
[0061] A. Under normal temperature and pressure, the exhaust gas containing hydrogen sulfide with a concentration of 3500ppm and carbon disulfide with a concentration of 4100ppm is directly input into the alkali spray to...
Embodiment 2
[0082] The technical principle involved in the present invention is to use the principle of acid-base neutralization to absorb hydrogen sulfide waste gas with lye, and then use the principle of evaporation, concentration and crystallization to make the absorption liquid into sodium sulfide. The principle of the chemical equation is as follows:
[0083] 2NaOH+H 2 S=Na 2 S+2H 2 o
[0084] From the recovery of hydrogen sulfide waste gas to the production of sodium sulfide or sodium hydrosulfide, the overall process is as follows figure 1 As shown, when the absorption liquid is evaporatively cooled and crystallized, the process steps are implemented figure 2 shown.
[0085] Below is a further description of the present invention, and the concrete steps are:
[0086] A. Under normal temperature and pressure, the exhaust gas containing hydrogen sulfide with a concentration of 3700ppm and carbon disulfide with a concentration of 3800ppm is directly input into the alkali spray ...
Embodiment 3
[0106] The technical principle involved in the present invention is to use the principle of acid-base neutralization to absorb hydrogen sulfide waste gas with lye, and then use the principle of evaporation, concentration and crystallization to make the absorption liquid into sodium sulfide. The principle of the chemical equation is as follows:
[0107] 2NaOH+H 2 S=Na 2 S+2H 2 o
[0108] From the recovery of hydrogen sulfide waste gas to the production of sodium sulfide or sodium hydrosulfide, the overall process is as follows figure 1 As shown, when the absorption liquid is evaporatively cooled and crystallized, the process steps are implemented figure 2 shown.
[0109] Below is a further description of the present invention, and the concrete steps are:
[0110] A. Under normal temperature and pressure, the exhaust gas containing hydrogen sulfide with a concentration of 3800ppm and carbon disulfide with a concentration of 3600ppm is directly input into the alkali spray ...
PUM
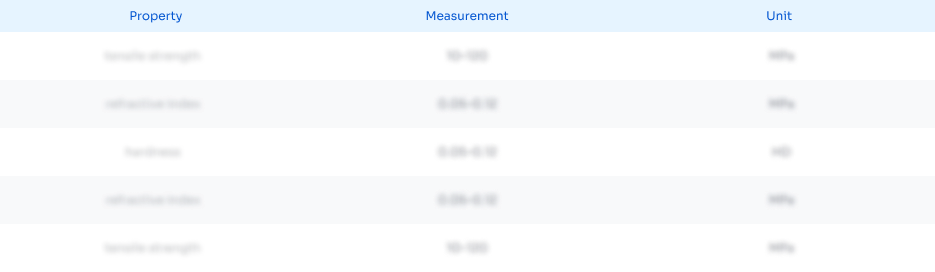
Abstract
Description
Claims
Application Information

- R&D
- Intellectual Property
- Life Sciences
- Materials
- Tech Scout
- Unparalleled Data Quality
- Higher Quality Content
- 60% Fewer Hallucinations
Browse by: Latest US Patents, China's latest patents, Technical Efficacy Thesaurus, Application Domain, Technology Topic, Popular Technical Reports.
© 2025 PatSnap. All rights reserved.Legal|Privacy policy|Modern Slavery Act Transparency Statement|Sitemap|About US| Contact US: help@patsnap.com