Device for reducing thrust and vibration at pipeline ends
An end thrust and pipeline technology, applied in the field of measurement and control, can solve the problems of easy vibration, high design and processing requirements, and reduced airflow quality, so as to meet the needs of thrust measurement, reduce pipe end thrust and coupled vibration. the effect of
- Summary
- Abstract
- Description
- Claims
- Application Information
AI Technical Summary
Problems solved by technology
Method used
Image
Examples
Embodiment
[0036] This embodiment is applied in the ramjet ground simulation test for measuring the thrust of the ramjet with high precision.
[0037] Refer to attached figure 1 A device for reducing the thrust and vibration at the end of the pipeline according to the present invention includes a movable buoy support assembly and a buffer cabin 16 .
[0038] Refer to attached figure 1 And attached figure 2 , the movable floating platform supporting assembly includes a load-bearing box 23, a movable platform 15, a supporting spring 6, an air spring and an air spring height control component. The load-bearing box is a square structure with an open end, and a connecting seat 4 is fixed on each of the four side walls of the load-bearing box, and the four connecting seats are located at the four corners of the load-bearing box. A connecting seat guide rod is fixed on the top.
[0039] The movable platform is placed at one end of the opening of the load-bearing box, and two slide grooves ...
PUM
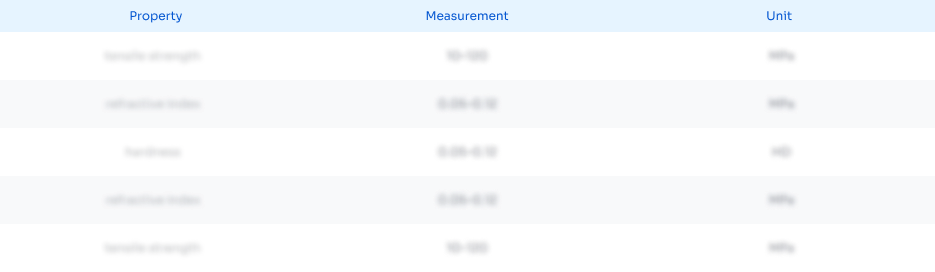
Abstract
Description
Claims
Application Information

- R&D Engineer
- R&D Manager
- IP Professional
- Industry Leading Data Capabilities
- Powerful AI technology
- Patent DNA Extraction
Browse by: Latest US Patents, China's latest patents, Technical Efficacy Thesaurus, Application Domain, Technology Topic, Popular Technical Reports.
© 2024 PatSnap. All rights reserved.Legal|Privacy policy|Modern Slavery Act Transparency Statement|Sitemap|About US| Contact US: help@patsnap.com