Binder used for pigment printing of textiles and preparation method thereof
A pigment printing and adhesive technology, which is applied in the field of adhesives for textile pigment printing and its preparation, can solve problems such as free formaldehyde release, achieve high crosslinking strength, excellent fastness, and improve the effect of soaping fastness
- Summary
- Abstract
- Description
- Claims
- Application Information
AI Technical Summary
Problems solved by technology
Method used
Image
Examples
Embodiment 1
[0034] ① Dissolve 0.8 grams of sodium lauryl sulfate in 25 grams of deionized water, add to an emulsification kettle, add 2.5 grams of fatty alcohol polyoxyethylene ether sodium sulfate, 1.4 grams of diethylaminoethyl methacrylate, and methyl acetoacetate Add 1.2 grams of ethyl acrylate, 0.6 grams of acrylic acid, 2 grams of styrene, 22.3 grams of butyl acrylate, 5.2 grams of ethyl acrylate, and 4 grams of methyl acrylate into the emulsification kettle, stir and emulsify to make a pre-emulsion;
[0035] ② Dissolve 0.6 g of ammonium persulfate in 6 g of deionized water to prepare an initiator solution for use;
[0036] 3. Add 27 grams of deionized water to the reactor, heat up to 85-95°C, add 15% of the total mass of the pre-emulsion prepared in step 1 to the reactor, and then add 2.5% of the total mass of the initiator solution prepared in step 2. 33%, start polymerization reaction;
[0037] ④ After 20 minutes, add the remaining emulsion prepared in step ① and the remaining i...
Embodiment 2
[0040] ①Dissolve 0.7 g of sodium lauryl sulfate in 25 g of deionized water, add to an emulsification kettle, add 2.8 g of fatty alcohol polyoxyethylene ether sodium sulfate, 1.3 g of diethylaminoethyl methacrylate, and methyl acetoacetate Add 1.3 grams of ethyl acrylate, 0.5 grams of acrylic acid, 5 grams of styrene, 24.4 grams of butyl acrylate, 3 grams of 2-ethylhexyl acrylate, and 1 gram of methyl acrylate into the emulsification kettle, stir and emulsify to make a pre-emulsion ;
[0041] ② Dissolve 0.7 g of ammonium persulfate in 7 g of deionized water to make an initiator solution for use.
[0042] 3. Add 27 grams of deionized water to the reactor, heat up to 85-95°C, add 20% of the total mass of the pre-emulsion prepared in step 1 to the reactor, and then add 20% of the total mass of the initiator solution prepared in step 2. 40%, start the polymerization reaction;
[0043] ④ After 20 minutes, add the remaining emulsion prepared in step ① and the remaining initiator so...
Embodiment 3
[0046] ① Dissolve 0.6 grams of sodium lauryl sulfate in 27 grams of deionized water, add to an emulsification kettle, add 3 grams of fatty alcohol polyoxyethylene ether sodium sulfate, 1.6 grams of diethylaminoethyl methacrylate, and methyl acetoacetate Add 1.2 grams of ethyl acrylate, 0.6 grams of acrylic acid, 4 grams of styrene, 23.2 grams of butyl acrylate, 4 grams of 2-ethylhexyl acrylate, and 2 grams of methyl acrylate into the emulsification kettle, stir and emulsify to make a pre-emulsion ;
[0047] ② Dissolve 0.8 g of ammonium persulfate in 8 g of deionized water to prepare an initiator solution for use.
[0048] 3. Add 23 grams of deionized water to the reactor, heat up to 85-95°C, add 20% of the total mass of the pre-emulsion prepared in step 1 to the reactor, and then add 20% of the total mass of the initiator solution prepared in step 2. 40%, start the polymerization reaction;
[0049] ④ After 20 minutes, add the remaining emulsion prepared in step ① and the rem...
PUM
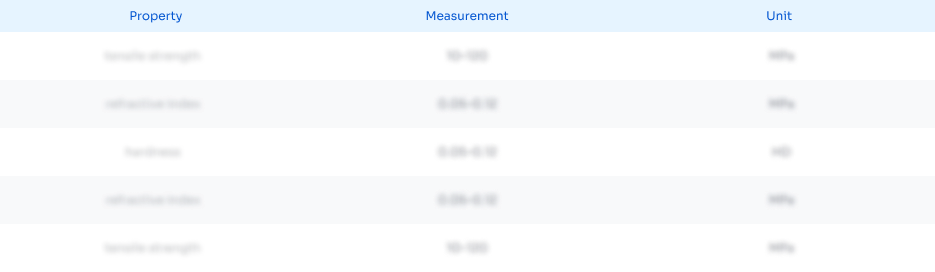
Abstract
Description
Claims
Application Information

- R&D Engineer
- R&D Manager
- IP Professional
- Industry Leading Data Capabilities
- Powerful AI technology
- Patent DNA Extraction
Browse by: Latest US Patents, China's latest patents, Technical Efficacy Thesaurus, Application Domain, Technology Topic, Popular Technical Reports.
© 2024 PatSnap. All rights reserved.Legal|Privacy policy|Modern Slavery Act Transparency Statement|Sitemap|About US| Contact US: help@patsnap.com