Continuous microwave curing production line for rubber cables
A technology of microwave vulcanization and rubber cable, applied in the field of continuous microwave vulcanization production line of rubber cable, can solve the problems of inability to obtain high-density rubber products, difficult to achieve linkage production, slow heat transfer rate inward, etc., to improve labor production conditions, The effect of shortening rubber vulcanization time and saving labor
- Summary
- Abstract
- Description
- Claims
- Application Information
AI Technical Summary
Problems solved by technology
Method used
Image
Examples
Embodiment Construction
[0015] like figure 1 As shown, the rubber cable continuous microwave vulcanization production line includes active pay-off machine 1, horizontal wire storage device 2, upper tractor 3, co-extrusion die head 4, automatic upper sealer 5, high-temperature setting equipment 6, microwave vulcanization section 7. Hot air vulcanization section 8, midpoint controller 9, automatic lower sealer 10, cooling section 11, traction machine 12 and wire arranging machine 13, active wire unwinding machine 1, horizontal wire storage device 2, upper traction machine 3 , co-extrusion die head 4, automatic upper sealer 5, high temperature setting equipment 6, microwave vulcanization section 7, hot air vulcanization section 8, midpoint controller 9, automatic lower sealer 10, cooling section 11, tractor 12 and The wiring machine 13 is connected sequentially, the automatic upper sealer 5 is installed at the entrance of the high temperature setting equipment 6, the automatic lower sealer 10 is install...
PUM
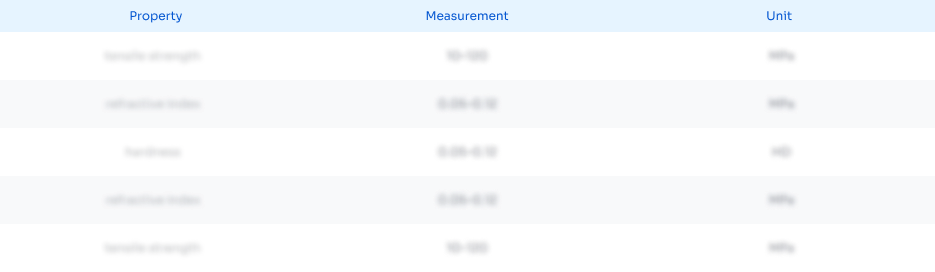
Abstract
Description
Claims
Application Information

- R&D Engineer
- R&D Manager
- IP Professional
- Industry Leading Data Capabilities
- Powerful AI technology
- Patent DNA Extraction
Browse by: Latest US Patents, China's latest patents, Technical Efficacy Thesaurus, Application Domain, Technology Topic, Popular Technical Reports.
© 2024 PatSnap. All rights reserved.Legal|Privacy policy|Modern Slavery Act Transparency Statement|Sitemap|About US| Contact US: help@patsnap.com