Method for preparing white carbon black by utilizing waste silicon rubber cracked residues
A white carbon black and residue technology, applied in the field of white carbon black preparation, can solve the problems of narrow application range of recycled products, poor product color, large ash particle size, etc., to avoid secondary pollution, narrow particle size distribution, good whiteness effect
- Summary
- Abstract
- Description
- Claims
- Application Information
AI Technical Summary
Problems solved by technology
Method used
Image
Examples
Embodiment 1
[0025] Example 1: 70g of the pyrolysis residue was crushed and sieved to 200 mesh, and calcined in a muffle furnace at 700-900°C for more than 2 hours to obtain 42g of white ash, the ash containing 76% silica mass fraction , respectively add 42g of calcined ash to the alkali-dissolved reaction kettle, add 7.09g of solid sodium hydroxide according to the molar ratio of silicon dioxide and solid sodium hydroxide in the ash to 3:1, and add 7.09g of solid sodium hydroxide according to the solid-to-liquid volume ratio of 1:2.2 Add 170ml of deionized water, carry out normal pressure reaction at 90°C for 5-7 hours, filter after the reaction, the filtrate is sodium silicate solution, analyze the concentration and modulus of the obtained sodium silicate solution, and dilute it with deionized water Sodium silicate solution to 1mol / L. Add 12g of 1% polyethylene glycol to the sol-gel reaction kettle, raise the temperature to 40°C, and under strong stirring, add 100ml of 1mol / L sodium sili...
Embodiment 2
[0027] 200g of pyrolysis residue was crushed and sieved to 200 mesh, and calcined in a muffle furnace at 900°C for more than 3 hours to obtain 118g of white ash. The mass fraction of silicon dioxide in the ash was 78%. Add 118g of ash slag after calcination, add 20g of solid sodium hydroxide according to the molar ratio of silicon dioxide and solid sodium hydroxide in the ash slag is 2.9:1, add 480ml of deionized water according to the solid-liquid volume ratio of 1:3, in Under the condition of 95℃, carry out the reaction under normal pressure for 3~5 hours. After the reaction, filter, the filtrate is sodium silicate solution, analyze the concentration and modulus of the obtained sodium silicate solution, and dilute the sodium silicate solution with deionized water to 1.1mol / L; Add 20g of 1.5% polyethylene glycol to the sol-gel reaction kettle, heat up to 45°C, and add 1.1mol / L sodium silicate obtained by alkali dissolution reaction dropwise to the solution under strong stirri...
PUM
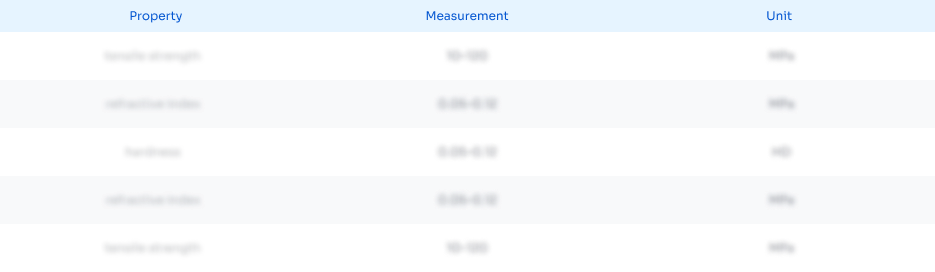
Abstract
Description
Claims
Application Information

- R&D
- Intellectual Property
- Life Sciences
- Materials
- Tech Scout
- Unparalleled Data Quality
- Higher Quality Content
- 60% Fewer Hallucinations
Browse by: Latest US Patents, China's latest patents, Technical Efficacy Thesaurus, Application Domain, Technology Topic, Popular Technical Reports.
© 2025 PatSnap. All rights reserved.Legal|Privacy policy|Modern Slavery Act Transparency Statement|Sitemap|About US| Contact US: help@patsnap.com