Process for controlling machining deformation of L-shaped aluminum alloy thin-wall end frames
A technology for processing deformation and aluminum alloy, which is applied in the field of end frame processing of forgings or blanks, and can solve problems such as inability to guarantee use requirements, poor roundness, uneven wall thickness, etc.
- Summary
- Abstract
- Description
- Claims
- Application Information
AI Technical Summary
Problems solved by technology
Method used
Image
Examples
example 1
[0034] like figure 1 The typical part shown is the L-shaped aluminum alloy thin-walled end frame 4, and the blank is shown in the figure image 3 (die forging), the turning process is as follows:
[0035] Vertical lathe flat ends (rough datum)—horizontal lathe processing inner shape (rough and semi-finishing)—vertical lathe flat large end face (semi-finishing)—horizontal lathe processing inner shape to size (finishing)—vertical lathe Flat large end face (finishing).
[0036] 1) Rough datum machining of flat end faces of vertical lathe: install the parts to be processed on the vertical lathe, such as Figure 8 , 9 As shown, according to the total machining allowance of 5mm, the roundness of the part is corrected, and the roundness error of the correcting is Figure 10 As shown, it includes a baffle 1 and fastening bolts 2. The baffle 1 is fixed on the machine table 3 through the fastening bolts 2, and the baffle 1 squeezes the L-shaped aluminum alloy thin-walled end frame 4 ...
example 2
[0043] like image 3 The typical part shown is the L-shaped aluminum alloy thin-walled end frame, and the blank is shown in the figure Image 6 , 7 (die forgings), the turning process is as follows:
[0044] Vertical lathe flat ends (rough datum)—horizontal lathe processing inner shape (rough and semi-finishing)—vertical lathe flat large end face (semi-finishing)—horizontal lathe processing inner shape to size (finishing)—vertical lathe Flat large end face (finishing).
[0045] 1) Rough datum machining of flat end faces of vertical lathe: install the parts to be processed on the vertical lathe, such as Figure 8 , as shown in 9, according to the total machining allowance of 3mm, the roundness of the parts is corrected, and the roundness error of the correction is Figure 10 ; Control the extrusion deformation of the part <0.5mm; set an anti-rotation hole at the part that is subsequently processed by the blank of the part, and install an anti-rotation pin in the anti-rotation...
PUM
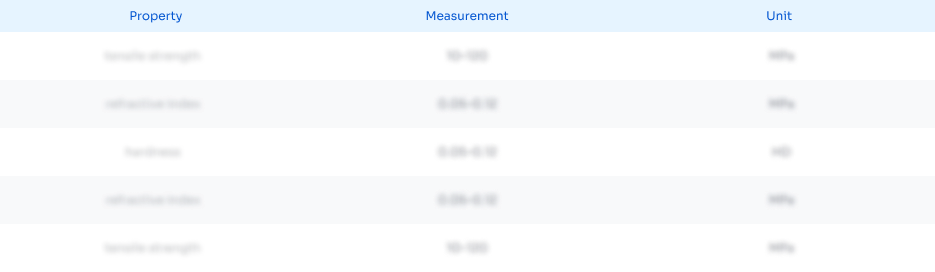
Abstract
Description
Claims
Application Information

- R&D
- Intellectual Property
- Life Sciences
- Materials
- Tech Scout
- Unparalleled Data Quality
- Higher Quality Content
- 60% Fewer Hallucinations
Browse by: Latest US Patents, China's latest patents, Technical Efficacy Thesaurus, Application Domain, Technology Topic, Popular Technical Reports.
© 2025 PatSnap. All rights reserved.Legal|Privacy policy|Modern Slavery Act Transparency Statement|Sitemap|About US| Contact US: help@patsnap.com