Ferrite heat resistant steel
A technology of heat-resistant steel and ferrite, applied in the field of ferritic heat-resistant steel, can solve the problems of unattainable high temperature performance, unsatisfactory comprehensive performance of alloy materials, and difficulty in ensuring alloy strength and toughness.
- Summary
- Abstract
- Description
- Claims
- Application Information
AI Technical Summary
Problems solved by technology
Method used
Image
Examples
Embodiment 1
[0038] Example 1: According to the chemical composition in Table 2, the ingot was smelted by vacuum induction + electroslag, and the steel ingot was heated and forged at 1170°C to form a bar. Ferritic heat-resistant steel, its mechanical properties at room temperature are shown in Table 3. It can be seen that the properties of the ferritic heat-resistant steel material of the present invention all reach Rm≥960Mpa, Rp0.2≥700Mpa, A≥15%, Z≥60%, HBW≤360, AKv≥58J.
Embodiment 2
[0039] Example 2: According to the chemical composition in Table 2, the ingot was smelted by vacuum induction + electroslag, the steel ingot was heated and forged at 1150°C to form a bar, and the bar was sampled and oil quenched at 1120°C and tempered at 740°C / 2 hours to obtain The mechanical properties of ferritic heat-resistant steel at room temperature are shown in Table 3.
Embodiment 3
[0040] Example 3: According to the chemical composition in Table 2, the ingot was smelted by vacuum induction + electroslag, the steel ingot was heated and forged at 1160°C to form a bar, and the bar was sampled after oil quenching at 1130°C and tempered at 730°C / 3 hours to obtain The mechanical properties of ferritic heat-resistant steel at room temperature are shown in Table 3.
PUM
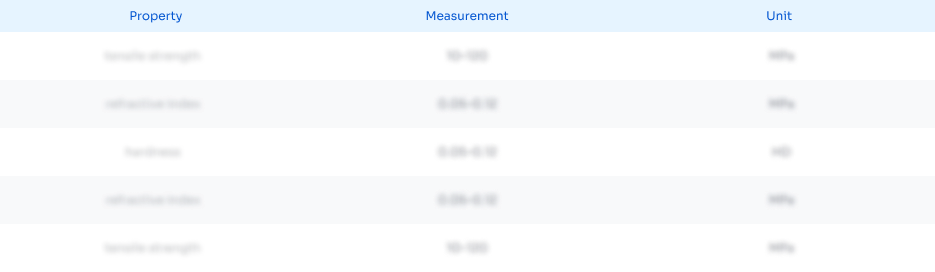
Abstract
Description
Claims
Application Information

- R&D Engineer
- R&D Manager
- IP Professional
- Industry Leading Data Capabilities
- Powerful AI technology
- Patent DNA Extraction
Browse by: Latest US Patents, China's latest patents, Technical Efficacy Thesaurus, Application Domain, Technology Topic, Popular Technical Reports.
© 2024 PatSnap. All rights reserved.Legal|Privacy policy|Modern Slavery Act Transparency Statement|Sitemap|About US| Contact US: help@patsnap.com