Direct current feed type motor testing system
A technology for motor testing and power feeding, applied in the direction of motor generator testing, etc., can solve the problems of power grid harmonic interference, complex control, and low control accuracy, and achieve the effect of reducing power supply capacity and improving system efficiency.
- Summary
- Abstract
- Description
- Claims
- Application Information
AI Technical Summary
Problems solved by technology
Method used
Image
Examples
Embodiment Construction
[0007] Such as figure 1 As shown, the present invention is at least provided with a first AC / DC converter 2 and a second AC / DC converter 3 , a generator 7 , and a rotational speed torque sensor 6 .
[0008] The input terminals of the first AC / DC converter 2 and the second AC / DC converter 3 are respectively connected to the grid AC input bus 1, and the DC output terminal of the first AC / DC converter 2 is connected to the DC of the motor 5 under test. Bus input 4.
[0009] The DC output terminal of the second AC / DC converter 3 is connected in series with the output terminal of the generator 7 to the DC bus input terminal 4 of the motor 5 under test.
[0010] The rotational speed and torque sensors 6 are coaxially connected between the tested motor 5 and the generator 7 through shaft couplings.
[0011] The signal output end of the rotational speed torque sensor 6 is connected to instruments, meters and a computer 8 for displaying various parameters of the motor under test.
PUM
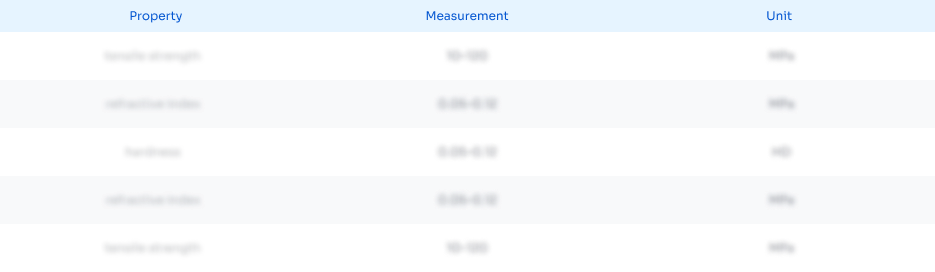
Abstract
Description
Claims
Application Information

- R&D
- Intellectual Property
- Life Sciences
- Materials
- Tech Scout
- Unparalleled Data Quality
- Higher Quality Content
- 60% Fewer Hallucinations
Browse by: Latest US Patents, China's latest patents, Technical Efficacy Thesaurus, Application Domain, Technology Topic, Popular Technical Reports.
© 2025 PatSnap. All rights reserved.Legal|Privacy policy|Modern Slavery Act Transparency Statement|Sitemap|About US| Contact US: help@patsnap.com