Flexible parallelogram mechanism based force sensor realizing two-stage force resolutions
A parallelogram and force sensor technology, applied in the field of force sensors, can solve the problems of limited measurement range, great influence of environmental noise, limited measurement range of force sensor accuracy and resolution, etc., and achieve less components, simple structure, and high measurement accuracy high effect
- Summary
- Abstract
- Description
- Claims
- Application Information
AI Technical Summary
Problems solved by technology
Method used
Image
Examples
Embodiment Construction
[0051] The present invention will be further described in detail below in conjunction with the accompanying drawings.
[0052] The material of the substrate 1 of the force sensor designed in the present invention is aluminum alloy 7075, which is processed by wire electric discharge cutting. It is mainly formed by overlapping two groups of flexible parallelogram linear motion mechanisms. In addition, the symmetrical arrangement of the two groups of flexible mechanisms ensures the high-precision linear motion of the intermediate platform, that is, reduces the parasitic error of the mechanism. At the same time, the main body of the sensor structure is a part, which does not need to be assembled, thus effectively avoiding problems such as friction and clearance caused by assembly of traditional force sensors. The biggest feature of this sensor is that it can effectively achieve two-level force resolution, which cannot be achieved by traditional force sensors. Since the sensor ut...
PUM
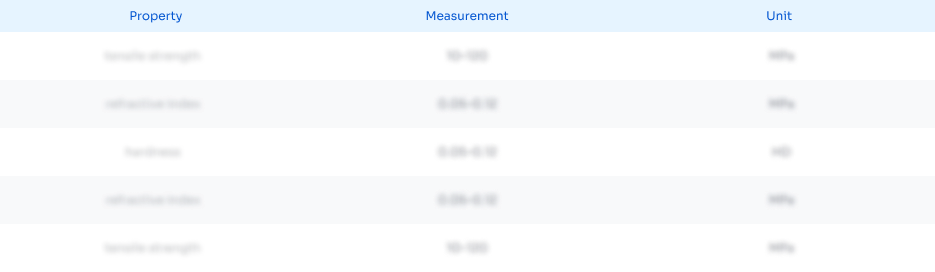
Abstract
Description
Claims
Application Information

- Generate Ideas
- Intellectual Property
- Life Sciences
- Materials
- Tech Scout
- Unparalleled Data Quality
- Higher Quality Content
- 60% Fewer Hallucinations
Browse by: Latest US Patents, China's latest patents, Technical Efficacy Thesaurus, Application Domain, Technology Topic, Popular Technical Reports.
© 2025 PatSnap. All rights reserved.Legal|Privacy policy|Modern Slavery Act Transparency Statement|Sitemap|About US| Contact US: help@patsnap.com