Parallel two-degree-of-freedom precision motion execution mechanism based on flexible hinge
A flexible hinge and precision motion technology, applied in the direction of supporting machines, mechanical equipment, transmission devices, etc., can solve the problems that cannot meet the needs of large-stroke motion occasions, it is difficult to achieve high-precision motion control, and the complexity of the motion control system, etc., to achieve reduction Effects of motion interference, reasonable configuration design, and simple control system requirements
- Summary
- Abstract
- Description
- Claims
- Application Information
AI Technical Summary
Problems solved by technology
Method used
Image
Examples
Embodiment Construction
[0032] In order to make the purpose, technical solution and advantages of the present invention clearer, the technical solution of the present invention will be described in detail below. Apparently, the described embodiments are only some of the embodiments of the present invention, but not all of them. Based on the embodiments of the present invention, all other implementations obtained by persons of ordinary skill in the art without making creative efforts fall within the protection scope of the present invention.
[0033] In describing the present invention, it is to be understood that the terms "central", "lateral", "length", "width", "height", "upper", "lower", "front", "rear", The orientation or positional relationship indicated by "left", "right", "vertical", "horizontal", "top", "bottom", "inner", "outer" and "side" are based on the attached figure 1 The orientations or positional relationships shown are only for the convenience of describing the present invention an...
PUM
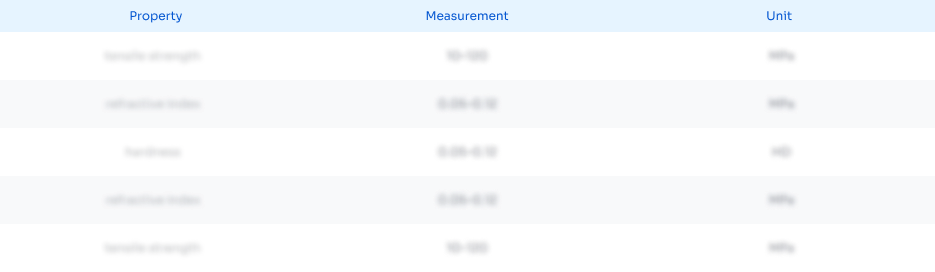
Abstract
Description
Claims
Application Information

- Generate Ideas
- Intellectual Property
- Life Sciences
- Materials
- Tech Scout
- Unparalleled Data Quality
- Higher Quality Content
- 60% Fewer Hallucinations
Browse by: Latest US Patents, China's latest patents, Technical Efficacy Thesaurus, Application Domain, Technology Topic, Popular Technical Reports.
© 2025 PatSnap. All rights reserved.Legal|Privacy policy|Modern Slavery Act Transparency Statement|Sitemap|About US| Contact US: help@patsnap.com