Flexible Roberts mechanism based force sensor realizing two-stage force resolutions
A force sensor and resolution technology, applied in the field of force sensors with two-level force resolution, can solve the problem of limited measurement range of force sensor accuracy and resolution, inability to achieve two-level or even multi-level force resolution, and reduced sensor measurement range and other problems, to achieve the effect of high measurement accuracy, simple structure, and fewer components
- Summary
- Abstract
- Description
- Claims
- Application Information
AI Technical Summary
Problems solved by technology
Method used
Image
Examples
Embodiment Construction
[0043] The present invention will be further described in detail below in conjunction with the accompanying drawings.
[0044] see figure 1 , Figure 1A , Figure 1B As shown, the present invention is a force sensor with two-stage force resolution based on a flexible Roberts mechanism. The force sensor includes a sensitive body 1 , a bracket 2 , a displacement detection part 3 , an eddy current displacement sensor 4 and a probe 5 .
[0045] The bracket 2 is installed on the third platform 14 of the sensitive body 1, that is, the bracket 2 is fixedly mounted on the third platform 14 of the sensitive body 1 through the cooperation of the B screw 106A and the E threaded hole 106, and the cooperation of the C screw 107A and the F threaded hole 107. Three platforms 14 on one side.
[0046] The displacement detection part 3 is installed on the first platform 12 of the sensitive body 1, that is, through the cooperation of the D screw 108A and the G threaded hole 108, and the coope...
PUM
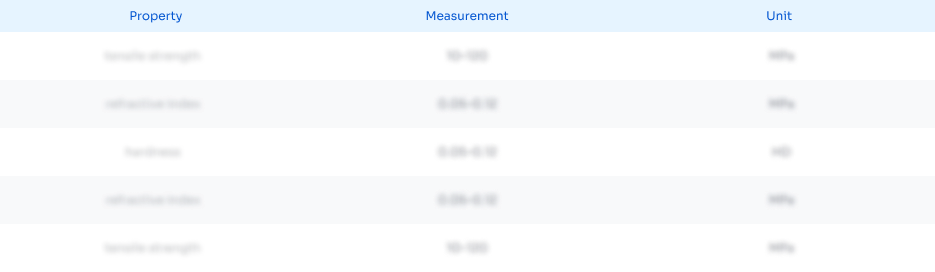
Abstract
Description
Claims
Application Information

- Generate Ideas
- Intellectual Property
- Life Sciences
- Materials
- Tech Scout
- Unparalleled Data Quality
- Higher Quality Content
- 60% Fewer Hallucinations
Browse by: Latest US Patents, China's latest patents, Technical Efficacy Thesaurus, Application Domain, Technology Topic, Popular Technical Reports.
© 2025 PatSnap. All rights reserved.Legal|Privacy policy|Modern Slavery Act Transparency Statement|Sitemap|About US| Contact US: help@patsnap.com