Sludge pyrolytic digestion process for efficiently recovering heat energy and equipment thereof
A technology for recovering heat energy and sludge, which is applied in the direction of pyrolysis sludge treatment, sludge treatment, biological sludge treatment, etc., which can solve the problems of heat loss and heat energy consumption, reduce sludge volume, ensure stability and high efficiency performance, and the effect of improving anaerobic digestion performance
- Summary
- Abstract
- Description
- Claims
- Application Information
AI Technical Summary
Problems solved by technology
Method used
Image
Examples
Embodiment 1
[0031] The remaining sludge after aerobic treatment (with a moisture content above 99%) is first pre-dehydrated by a centrifugal separator or a belt dryer to a moisture content of 80%, and the pre-dehydrated sludge enters the sludge storage tank to be separated from the rest The reflux sludge is mixed, and the mixed sludge enters the hydrolysis reactor A after passing through the crusher, and is heated and pressurized to 150°C and 0.5Mpa by injecting hot steam (in the sludge heating stage of the hydrolysis reactor A, the hydrolysis reactor B starts to material), thermally hydrolyzed for 60min.
[0032] After the hydrolysis reaction in the hydrolysis reactor A is completed, the hot steam enters the hydrolysis reactor B through the steam pipeline for preheating. Spray into flash tank. The sludge after thermal hydrolysis is further released in the flash tank, and the released hot steam is returned to the hydrolysis reactor B for preheating.
[0033]The temperature and pressure ...
Embodiment 2
[0035] The remaining sludge after aerobic treatment (with a water content above 99%) is pre-dehydrated with a centrifugal separator or a belt dryer to a water content of 78%, and the pre-dehydrated sludge enters the sludge storage tank and is mixed with the rest The reflux sludge is mixed, and the mixed sludge enters the hydrolysis reactor A after passing through the crusher, and is heated and pressurized to 180°C and 0.7Mpa by injecting hot steam (the sludge heating stage in the hydrolysis reactor A, and the hydrolysis reactor B starts Feeding), thermal hydrolysis 30min.
[0036] After the hydrolysis reaction in the hydrolysis reactor A is completed, the hot steam enters the hydrolysis reactor B through the steam pipeline for preheating. Spray into flash tank. The thermally hydrolyzed sludge is further released in the flash tank, and the released hot steam is returned to reactor B for preheating.
[0037] The temperature and pressure in the hydrolysis reactor B reached 180°...
Embodiment 3
[0039] The remaining sludge after aerobic treatment (with a water content above 99%) is pre-dehydrated with a centrifugal separator or a belt dryer until the water content is 75%, and the pre-dehydrated sludge enters the sludge storage tank and is mixed with the rest The reflux sludge is mixed, and the mixed sludge enters the hydrolysis reactor A after passing through the crusher, and is heated and pressurized to 165°C and 0.6Mpa by injecting hot steam (the sludge heating stage in the hydrolysis reactor A, and the hydrolysis reactor B starts Feeding), thermal hydrolysis 90min.
[0040] After the hydrolysis reaction in the hydrolysis reactor A is completed, the hot steam enters the hydrolysis reactor B through the steam pipeline for preheating. Spray into flash tank. The sludge after thermal hydrolysis is further released in the flash tank, and the released hot steam is returned to the hydrolysis reactor B for preheating.
[0041] The temperature and pressure in the hydrolysi...
PUM
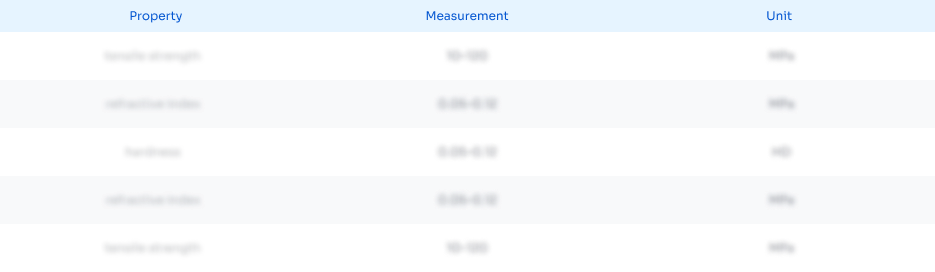
Abstract
Description
Claims
Application Information

- Generate Ideas
- Intellectual Property
- Life Sciences
- Materials
- Tech Scout
- Unparalleled Data Quality
- Higher Quality Content
- 60% Fewer Hallucinations
Browse by: Latest US Patents, China's latest patents, Technical Efficacy Thesaurus, Application Domain, Technology Topic, Popular Technical Reports.
© 2025 PatSnap. All rights reserved.Legal|Privacy policy|Modern Slavery Act Transparency Statement|Sitemap|About US| Contact US: help@patsnap.com