Composite type sacrificial anode for repairing reinforced concrete structures
A technology of reinforced concrete and sacrificial anode, which is applied in the field of corrosion and protection, can solve the problems of inability to effectively determine the protection area and construction area of reinforced concrete tidal zone and splash zone, and lack of research and development of sacrificial anode materials. Simple installation, wide application effect
- Summary
- Abstract
- Description
- Claims
- Application Information
AI Technical Summary
Problems solved by technology
Method used
Image
Examples
Embodiment 1
[0039] The composite sacrificial anode of the present invention is used for the repair of reinforced concrete in the full immersion area of the marine environment. The formula of the zinc alloy sacrificial anode 2 is Al: 0.35%, Mg: 0.3%, Si: 0.85%, Sn: 0.28%, and the impurity content: Fe≤0.005%, Cu≤0.005%, Pb≤0.01%, Cd≤0.003%, and the balance is Zn. Use a graphite crucible to melt the zinc ingot in the heating furnace, add Al, Mg, Si, and Sn to the molten zinc solution according to the proportion, stir with a graphite rod, remove the slag, and cast it into the spiral of the iron core 6 placed in advance. in the mold. The formula of the highly conductive cement colloid 1 is, Portland cement: sand: graphite: bentonite: lithium nitrate: polypropylene fiber: water = 1:0.95:0.1:0.15:0.06:0.006:0.5. Put the spiral sacrificial anode 2 into a rectangular filler mold, and according to the above formula, put the filler (high conductive cement colloid 1) into the mold, and after curin...
Embodiment 2
[0043] The composite sacrificial anode of the present invention is used for the repair of reinforced concrete in the tidal zone of the marine environment. The formula of the zinc alloy sacrificial anode 2 is Al: 0.65%, Mg: 0.48%, Si: 0.55%, Sn: 0.33%, and the impurity content: Fe≤0.005%, Cu≤0.005%, Pb≤0.01%, Cd≤0.003%, and the balance is Zn. Use a graphite crucible to melt the zinc ingot in a heating furnace, add Al, Mg, Si, and Sn to the molten zinc solution according to the ratio, stir with a graphite rod, remove the slag, and cast it into the spiral shape of the pre-placed iron core. in the mold. The formula of highly conductive cement colloid 1 is Portland cement: sand: coke: bentonite: lithium nitrate: polypropylene fiber: water = 1:0.85:0.15:0.18:0.10:0.005:0.85. Put the spiral sacrificial anode 2 into the rectangular filler mold, according to the above formula, put the highly conductive cement colloid 1 into the mold, and after curing, it is obtained. figure 2 The co...
Embodiment 3
[0047] The composite sacrificial anode of the present invention is used for the repair of reinforced concrete in atmospheric areas containing chlorine. The formula of the high-performance zinc alloy sacrificial anode is Al: 0.82%, Mg: 0.4%, Si: 0.5%, Sn: 0.6%, impurities Content: Fe≤0.005%, Cu≤0.005%, Pb≤0.01%, Cd≤0.003%, the balance is Zn. Use a graphite crucible to melt the zinc ingot in a heating furnace, add Al, Mg, Si, and Sn to the molten zinc solution according to the ratio, stir with a graphite rod, remove the slag, and cast it into the spiral shape of the pre-placed iron core. in the mold. The highly conductive cement colloid formula is Portland cement: sand: graphite: bentonite: lithium nitrate: polypropylene fiber: water = 1:0.65:0.14:0.2:0.010:0.008:0.65. Put the helical sacrificial anode into the filling body mold of the cylinder, according to the above formula, put the filling material into the mold, and after curing, you can get figure 1 The finished composite...
PUM
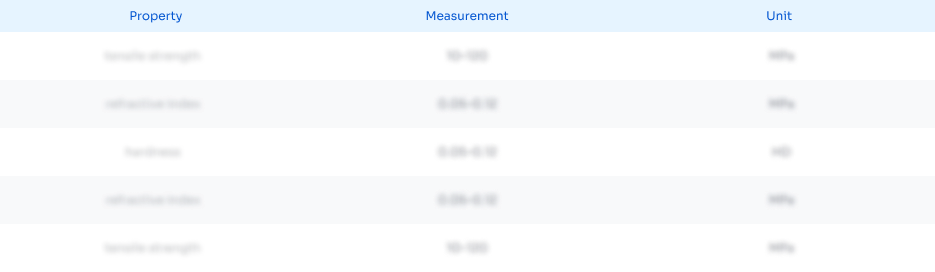
Abstract
Description
Claims
Application Information

- Generate Ideas
- Intellectual Property
- Life Sciences
- Materials
- Tech Scout
- Unparalleled Data Quality
- Higher Quality Content
- 60% Fewer Hallucinations
Browse by: Latest US Patents, China's latest patents, Technical Efficacy Thesaurus, Application Domain, Technology Topic, Popular Technical Reports.
© 2025 PatSnap. All rights reserved.Legal|Privacy policy|Modern Slavery Act Transparency Statement|Sitemap|About US| Contact US: help@patsnap.com