Method for second reduction and decarbonization of first reduced iron powder
A technology of reducing iron powder and decarburization, which is applied in the field of metallurgy, can solve problems such as unclean decarburization, high energy consumption, and difficult control of dew point, and achieve the effect of reducing procedures and broad application prospects
- Summary
- Abstract
- Description
- Claims
- Application Information
AI Technical Summary
Problems solved by technology
Method used
Image
Examples
Embodiment 1
[0022] Embodiment 1 Adopt the method of the present invention to carry out secondary reduction and decarburization of primary reduced iron powder
[0023] The primary reduced iron powder with a carbon content of 1.39 wt% was made to have a water content of 10 wt%, hydrogen was introduced, and the primary reduced iron powder was reacted with hydrogen at 810 ° C for 60 min, cooled, crushed and sieved to obtain secondary reduced iron powder .
[0024] The composition changes before and after reduction of iron powder are shown in Table 1.
Embodiment 2
[0025] Embodiment 2 Adopt the method of the present invention to carry out secondary reduction and decarburization of primary reduced iron powder
[0026] The primary reduced iron powder with a carbon content of 0.68 wt % is made to have a water content of 3.5 wt %, and decomposed ammonia gas is introduced to make the primary reduced iron powder react with the decomposed ammonia gas at 850 ° C for 30 minutes, and then cooled, crushed and sieved to obtain Secondary reduced iron powder.
[0027] The composition changes before and after reduction of iron powder are shown in Table 1.
[0028] Table 1 Composition changes before and after reduction of iron powder (wt%)
[0029]
PUM
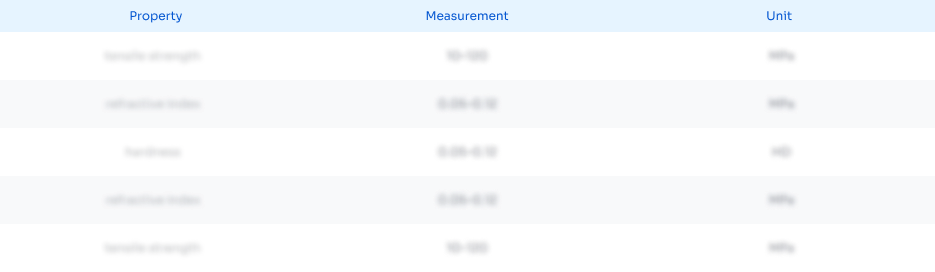
Abstract
Description
Claims
Application Information

- R&D
- Intellectual Property
- Life Sciences
- Materials
- Tech Scout
- Unparalleled Data Quality
- Higher Quality Content
- 60% Fewer Hallucinations
Browse by: Latest US Patents, China's latest patents, Technical Efficacy Thesaurus, Application Domain, Technology Topic, Popular Technical Reports.
© 2025 PatSnap. All rights reserved.Legal|Privacy policy|Modern Slavery Act Transparency Statement|Sitemap|About US| Contact US: help@patsnap.com