High temperature resistant catalyst for low concentration methane combustion and preparation method thereof
A methane combustion and catalyst technology, applied in chemical instruments and methods, physical/chemical process catalysts, metal/metal oxide/metal hydroxide catalysts, etc., can solve problems such as difficult and stable use, and achieve good thermal stability and Low temperature activity, simple preparation method and low pollution
- Summary
- Abstract
- Description
- Claims
- Application Information
AI Technical Summary
Problems solved by technology
Method used
Image
Examples
Embodiment 1
[0031] will contain 8.560g Y x Zr 1-x o 2-δ(x=0.09) powder precursor was added to 100ml of water, stirred with a homogenizer at 8000rpm for 10min to form a uniform and stable slurry, and then vigorously stirred with a stirring paddle for 0.5h. According to the general formula La 1-x Sr x mn 1-y Ni y o 3 (x=0.2, y=0.5) weigh 3.463g La(NO 3 ) 3 .6H 2 O, 0.423g Sr(NO 3 ) 2 , 1.789g 50%Mn(NO 3 ) 2 , 1.454g Ni(NO 3 ) 2 .6H 2 O was made into 100mL mixed aqueous solution; and 100mL NaOH aqueous solution containing 2.4g was added to the slurry at the same time, after vigorous stirring for 5h, filtered, the pH of the filtrate was 11.3. Rinse the filter cake until the filtrate is neutral; dry the filter cake at 120°C and roast at 900°C for 6 hours to obtain the catalyst, which is called Cat.1.
Embodiment 2
[0033] will contain 6.115g Y x Zr 1-x o 2-δ (x=0.08) powder precursor was added to 80ml of water, stirred with a homogenizer at 10000rpm for 5min, and then vigorously stirred with a stirring paddle for 0.5h. According to the general formula La 1-x Sr x mn 1-y Ni y o 3 (x=0.1, y=1) weigh 3.896g La(NO 3 ) 3 .6H 2 O, 0.212g Sr(NO 3 ) 2 , 2.907g Ni(NO 3 ) 2 .6H 2 O was made into 100mL mixed aqueous solution; and 100mL NaOH aqueous solution containing 2.4g was added to the slurry at the same time, after vigorous stirring for 5h, filtered, the pH of the filtrate was 11.9. Rinse the filter cake until the filtrate is neutral; dry the filter cake at 120°C and roast at 1100°C for 3 hours to obtain the catalyst, which is called Cat.2.
Embodiment 3
[0035] will contain 8.560g Y x Zr 1-x o 2-δ (x=0.09) powder precursor was added to 100ml of water, stirred with a homogenizer at 8000rpm for 10min, and then vigorously stirred with a stirring paddle for 0.5h. According to the general formula La 1-x Sr x mn 1-y Ni y o 3 (x=0.2, y=0.5) weigh 3.463g La(NO 3 ) 3 .6H 2 O, 0.423g Sr(NO 3 ) 2 , 1.789g 50%Mn(NO 3 ) 2 , 1.454g Ni(NO 3 ) 2 .6H 2 O was made into 100mL mixed aqueous solution; and 100mL NaOH aqueous solution containing 2.4g was added to the slurry at the same time, after vigorous stirring for 5h, filtered, the pH of the filtrate was 11.3. Rinse the filter cake until the filtrate is neutral; dry the filter cake at 120°C and roast at 1000°C for 4 hours to obtain the catalyst, which is called Cat.3.
PUM
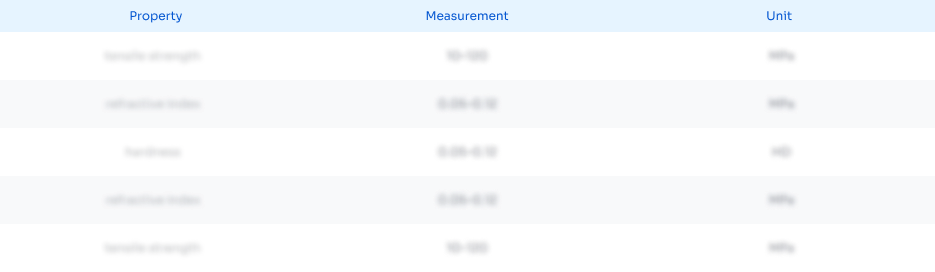
Abstract
Description
Claims
Application Information

- R&D
- Intellectual Property
- Life Sciences
- Materials
- Tech Scout
- Unparalleled Data Quality
- Higher Quality Content
- 60% Fewer Hallucinations
Browse by: Latest US Patents, China's latest patents, Technical Efficacy Thesaurus, Application Domain, Technology Topic, Popular Technical Reports.
© 2025 PatSnap. All rights reserved.Legal|Privacy policy|Modern Slavery Act Transparency Statement|Sitemap|About US| Contact US: help@patsnap.com