End milling cutter with equal actual rake angles and unequal spiral angles
A technology of helix angle and end mill, applied in the field of metal cutting, can solve problems such as the surface quality of workpiece affecting tool life, avoid wear or uneven chipping, prolong tool life and reduce cutting force.
- Summary
- Abstract
- Description
- Claims
- Application Information
AI Technical Summary
Problems solved by technology
Method used
Image
Examples
Embodiment Construction
[0017] figure 1 and figure 2 It shows an embodiment of an end mill with equal actual rake angle and unequal helix angle of the present invention. The end mill includes a cutting part 20 and a shank part 22. Helically extending chip flute 30, the surface of chip flute 30 facing the cutting rotation direction is rake face 32, rake face 32 intersects with the outer peripheral surface of the cutting part to form peripheral cutting edge 40, at least one of the peripheral cutting edges 40 has a different helix angle β is different from the helix angle β of other peripheral cutting edges 40, and the radial rake angle γ of at least one peripheral cutting edge 40 is different from the radial rake angle γ of other peripheral cutting edges 40, the actual rake angle γ of each peripheral cutting edge 40 n equal, so that the tool can eliminate resonance to a large extent during high-efficiency milling and reduce the surface roughness of the workpiece to be machined; at the same time, the ...
PUM
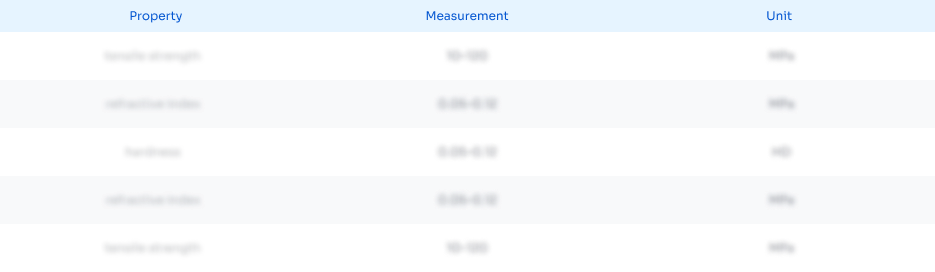
Abstract
Description
Claims
Application Information

- R&D
- Intellectual Property
- Life Sciences
- Materials
- Tech Scout
- Unparalleled Data Quality
- Higher Quality Content
- 60% Fewer Hallucinations
Browse by: Latest US Patents, China's latest patents, Technical Efficacy Thesaurus, Application Domain, Technology Topic, Popular Technical Reports.
© 2025 PatSnap. All rights reserved.Legal|Privacy policy|Modern Slavery Act Transparency Statement|Sitemap|About US| Contact US: help@patsnap.com