Quenching method for 20Cr13-40Cr13 martensite stainless steel
A martensitic stainless steel and quenching tank technology, applied in the field of metal heat treatment, can solve the problems of lack of quenching speed, workpiece explosion, insufficient oil quenching cooling speed, etc., and achieve the effect of eliminating the hidden danger of fire and oil fume pollution.
- Summary
- Abstract
- Description
- Claims
- Application Information
AI Technical Summary
Problems solved by technology
Method used
Image
Examples
Embodiment 1
[0028] 20Cr13 flat steel, the size is 40mm in thickness, 40mm in width, and 8.0m in length. Such as figure 2 As shown, the steel is heated with gas in a continuous roller hearth heating furnace, the furnace temperature is ≤200°C, the heating rate is ≤100°C / h, and it is heated to 970°C for austenitization and heat preservation for 1.5 hours; after the heat preservation is completed, the material is quickly discharged , enter the roller hearth quenching tank for water-air-controlled quenching (immersion solution 38S→air cooling 73S→immersion solution 31S), after the steel is air-cooled to below 155°C, enter the electric heating continuous roller hearth furnace for tempering, the tempering temperature 501°C for 8 hours; the hardness of the tempered steel reaches 33±1HRC, and the bending degree is not greater than 2.5mm / m. Pre-hardened 20Cr13 flat steel is used for moving blades.
Embodiment 2
[0030] 20Cr13 flat steel, the size is 90mm in thickness, 305mm in width, and 5.0m in length. Such as image 3 As shown, the steel is heated with gas in a continuous roller hearth heating furnace, the furnace temperature is ≤200°C, the heating rate is ≤100°C / h, and it is heated to 970°C for austenitization and heat preservation for 3 hours; after the heat preservation is completed, the material is quickly discharged , into the roller bottom quenching tank for water-air quenching (air cooling 48S→immersion liquid 38S→air cooling 88S→immersion liquid 53S→air cooling 92S→immersion liquid 34S→air cooling 72S→immersion liquid 36S→air cooling 60S→immersion liquid 20S ) after treatment, the steel is air-cooled to below 174°C and entered into an electric heating continuous roller hearth furnace for tempering at a tempering temperature of 504°C for 8 hours; the hardness of the tempered steel reaches 33±1HRC, and the bending degree is not greater than 2.5mm / m. Pre-hardened 20Cr13 flat s...
Embodiment 3
[0032] Y30Cr13 flat steel, the size is 40mm in thickness, 305mm in width, and 6.0m in length. Such as Figure 4 As shown, the steel is heated with gas in a continuous roller hearth heating furnace, the furnace temperature is ≤200°C, the heating rate is ≤100°C / h, and it is heated to 970°C for austenitization and heat preservation for 1.5 hours; after the heat preservation is completed, the material is quickly discharged , into the roller hearth quenching tank for water-air-controlled quenching (immersion liquid 38S→air cooling 73S→immersion liquid 28S) treatment, the steel is air-cooled to below 168°C and enters the electric heating continuous roller hearth furnace for tempering, tempering temperature 524°C for 8 hours; the hardness of the tempered steel reaches 34±1HRC, and the bending degree is not more than 2.5mm / m. Pre-hardened Y30Cr13 flat steel is used in hydraulic valve blocks.
PUM
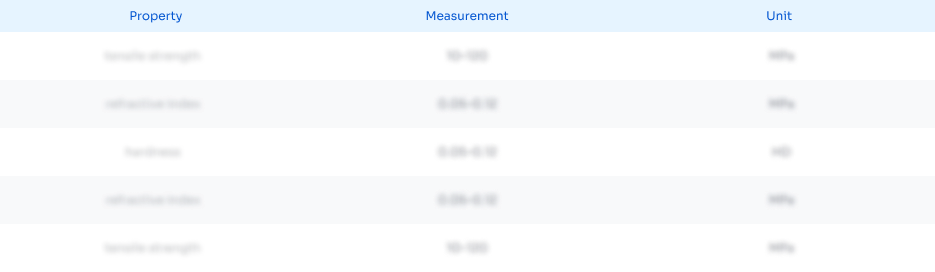
Abstract
Description
Claims
Application Information

- Generate Ideas
- Intellectual Property
- Life Sciences
- Materials
- Tech Scout
- Unparalleled Data Quality
- Higher Quality Content
- 60% Fewer Hallucinations
Browse by: Latest US Patents, China's latest patents, Technical Efficacy Thesaurus, Application Domain, Technology Topic, Popular Technical Reports.
© 2025 PatSnap. All rights reserved.Legal|Privacy policy|Modern Slavery Act Transparency Statement|Sitemap|About US| Contact US: help@patsnap.com