Hydrostatic test device used for large-diameter thick-wall pipe joint and hydrostatic test method thereof
A hydraulic test and pipe joint technology, applied in the direction of applying stable tension/pressure to test the strength of materials, pipes/pipe joints/fittings, measuring devices, etc., can solve the problem of heavy welding workload, increased forging cost, high forging cost, etc. problems, to achieve the effects of shortened production cycle, reduced production cost, and mature manufacturing process
- Summary
- Abstract
- Description
- Claims
- Application Information
AI Technical Summary
Problems solved by technology
Method used
Image
Examples
Embodiment 1
[0069] Such as figure 2 As shown, it is a structural cross-sectional view of a large-diameter thick-walled pipe joint 2. During forging, other structures of the large-diameter thick-walled pipe joint 2 are processed according to the design size, and only the inner diameter of the pipe joint 2 is kept close to the port. figure 2 As shown in bump 5, as Figure 4 As mentioned above, the protrusion 5 is processed into a circular truncated cone with a through hole in the middle and a certain thickness. When the sealing plate 3 is put into the pipe joint 2 through the pipeline body 1, the image 3 The sealing plate 3 and the protrusion 5 are welded at the position shown in , at this time, the weld seam 4 only acts as a seal, and the part of the protrusion 5 that is in contact with the sealing plate 3 bears the force exerted on the sealing plate 3 by the hydraulic test. Since the protrusion 5 is integrated with the pipe joint 2, it can bear a large force, which can prevent the se...
Embodiment 2
[0071] Such as Figure 5 As shown, it is a structural cross-sectional view of a large-diameter thick-walled pipe joint 2. During forging, other structures of the large-diameter thick-walled pipe joint 2 are processed according to the design size, and only the inner diameter of the pipe joint 2 is kept close to the port. Figure 5 For the protrusion 5 shown, when the sealing plate 3 cannot be put into the pipe joint 2 through the pipe body 1, the middle of the protrusion 5 is processed as Figure 6 Shown is a frustum of circular shape with a similar oval-shaped through-hole and a certain thickness. At this time, the shape of the sealing plate 3 which acts as a plug is similar to the shape of the through hole on the protrusion 5, which is similar to an ellipse. During hydrostatic testing, such as Figure 7 As shown, put the sealing plate 3 obliquely from the end of the pipe joint 2 port, and pass through the through hole on the protrusion 5 (such as Figure 8 shown), then rot...
Embodiment 3
[0073] Such as Figure 10 Shown, other steps are exactly the same as embodiment 2. When the direction of the pipe joint 2 is upward or other factors make it inconvenient for the sealing plate 3 to be in place, the auxiliary rod 6 can be connected to the sealing plate 3, and the sealing plate 3 can be moved from the end of the port of the pipe joint 2 by using the auxiliary rod 6. The plate 3 passes obliquely through the through hole on the protrusion 5, and then rotated 90° to be placed and then welded. After the hydrostatic test, the protrusion 5 is cut off, and the sealing plate 3 is separated from the pipe joint 2, and then the inner wall of the pipe joint 2 at the protrusion 5 is machined to the designed size. At the same time, the protrusion 5, the sealing plate 3, and the auxiliary rod 6 in place are separated, and the residual welding slag on the sealing plate 3 is removed. At this time, the sealing plate 3 and the auxiliary rod 6 in place can be reused.
PUM
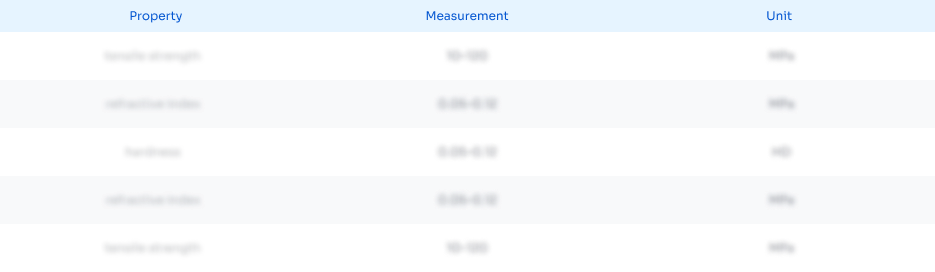
Abstract
Description
Claims
Application Information

- R&D
- Intellectual Property
- Life Sciences
- Materials
- Tech Scout
- Unparalleled Data Quality
- Higher Quality Content
- 60% Fewer Hallucinations
Browse by: Latest US Patents, China's latest patents, Technical Efficacy Thesaurus, Application Domain, Technology Topic, Popular Technical Reports.
© 2025 PatSnap. All rights reserved.Legal|Privacy policy|Modern Slavery Act Transparency Statement|Sitemap|About US| Contact US: help@patsnap.com