Dehydrogenation catalyst reduction method
A dehydrogenation catalyst, supported catalyst technology, applied in chemical instruments and methods, catalyst activation/preparation, physical/chemical process catalysts, etc. question
- Summary
- Abstract
- Description
- Claims
- Application Information
AI Technical Summary
Problems solved by technology
Method used
Image
Examples
preparation example Construction
[0014] The dehydrogenation catalyst can be prepared by a conventional method, such as using an impregnation method to support the dehydrogenation active metal, and the auxiliary agent can be introduced during the preparation of the alumina carrier and / or by an impregnation method.
[0015] In the dehydrogenation catalyst reduction method of the present invention, a specific dehydrogenation catalyst uses Sn-containing alumina as a carrier, and the dehydrogenation active metal component is generally selected from one or more of platinum, palladium, iridium, rhodium or osmium in the platinum group. There are several types, and the dosage is 0.01% to 2% of the weight of the carrier in terms of simple substances. The content of Sn is 0.1%-10% of the weight of the carrier in terms of simple substance. In the dehydrogenation catalyst with Sn-containing alumina as the carrier, Sn is introduced into the Sn-containing material when the alumina is gelled, and then made into a carrier. T...
example 1
[0033] Preparation of Sn-containing alumina support. After mixing a certain amount of 0.98M aluminum trichloride solution and 0.01M tin tetrachloride solution, add an appropriate amount of ammonia water with a mass concentration of 8%, mix evenly in a neutralization tank at 60-80°C, and control the pH value 7.0~9.0, after filtering, washing with water and acidifying, pressurize into spheres in oily ammonia column, dry, age, and roast at 650~750°C for 4 hours to obtain alumina pellets containing 0.3wt% Sn.
[0034] The alumina pellet carrier containing 0.3% Sn was calcined at 800°C for 3h, the calcined carrier was immersed in an aqueous solution containing chloroplatinic acid for 6h at 70°C, dried at 120°C for 2h, and calcined at 500°C for 4h. Then activate in air containing water vapor for 4h. Then at 70°C with KNO 3 Soaked in aqueous solution for 2h, dried and roasted under the same conditions. The loading amount of each component in the catalyst is: Pt 0.5wt%, Sn 0.3wt%, ...
example 2
[0046] Preparation of Sn-containing alumina support. After mixing a certain amount of 1.08M aluminum trichloride solution and 0.01M tin tetrachloride solution, add a certain amount of 10% ammonia water, mix evenly in a neutralization tank at 60-80°C, and control the pH value from 7.0 to 9.0, after filtering, washing with water and acidifying, pressurize into spheres in an oily ammonia column, dry, age, and roast at 650-750°C for 4 hours to obtain alumina pellets containing 1.0wt% Sn.
[0047] The alumina pellet carrier containing 1.0% Sn was calcined at 800°C for 3h, and the calcined carrier was immersed in an aqueous solution containing chloroplatinic acid for 4h at 70°C, dried at 120°C for 2h, and calcined at 500°C for 4h. Activation in air containing water vapor for 4h. Then at 70°C with KNO 3 Soaked in aqueous solution for 2 hours, dried and roasted under the same conditions, 400 ~ 550 ° C temperature program reduction, the heating rate is 2 ° C / min. The loading amoun...
PUM
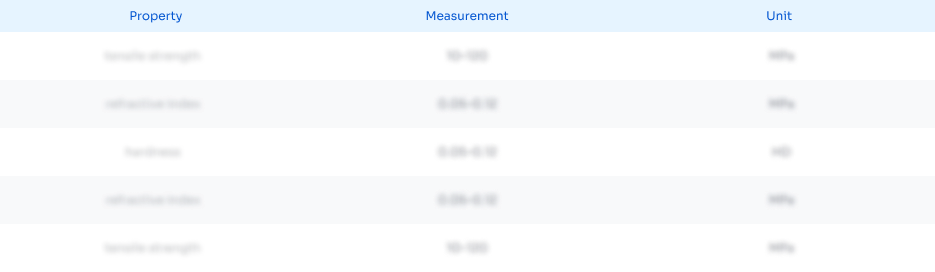
Abstract
Description
Claims
Application Information

- R&D
- Intellectual Property
- Life Sciences
- Materials
- Tech Scout
- Unparalleled Data Quality
- Higher Quality Content
- 60% Fewer Hallucinations
Browse by: Latest US Patents, China's latest patents, Technical Efficacy Thesaurus, Application Domain, Technology Topic, Popular Technical Reports.
© 2025 PatSnap. All rights reserved.Legal|Privacy policy|Modern Slavery Act Transparency Statement|Sitemap|About US| Contact US: help@patsnap.com