Chill coating for casting
A cold iron coating and casting technology, applied in the direction of coating, casting mold, casting mold composition, etc., can solve the problems of inconspicuous effect, increase of casting production cost, difficult to eliminate, etc., to reduce cost, improve casting yield, avoid white mouth effect
- Summary
- Abstract
- Description
- Claims
- Application Information
AI Technical Summary
Problems solved by technology
Method used
Examples
Embodiment 1
[0007] Embodiment 1: this chilled iron coating is made up of following material by weight percentage: graphite powder 88.5%, sodium bentonite 3%, iron oxide red powder 2.5%, ferrosilicon powder 2.5%, rosin 3.5%, ethanol amount; Shaped graphite powder and flaky graphite powder are used in combination, and the percentage by weight is: 30% of flaky graphite powder and 70% of amorphous graphite powder.
[0008] The configuration method of the coating: 1. Grind the rosin and pass through a 200 / 270 sieve; 2. Dissolve the rosin in ethanol, add bentonite and stir, then add scaly graphite powder, amorphous graphite powder, iron oxide red powder, silicon Iron powder, stir evenly for use. When using, brush evenly on the cold iron work surface with a row of brushes, with a thickness of about 0.1-0.3mm, and then ignite and bake.
Embodiment 2
[0009] Embodiment 2: this cold iron coating is made up of following material by weight percentage: graphite powder 89%, sodium bentonite 2%, iron oxide red powder 3%, ferrosilicon powder 3%, rosin 3%, ethanol amount; Amorphous graphite powder The ratio of flake graphite powder is 25:75.
Embodiment 3
[0010] Embodiment 3: this cold iron coating is made up of following material by weight percentage: graphite powder 88%, sodium bentonite 4%, iron oxide red powder 2%, ferrosilicon powder 2%, rosin 4%, ethanol amount; Amorphous graphite powder The ratio with flake graphite powder is 35:65.
PUM
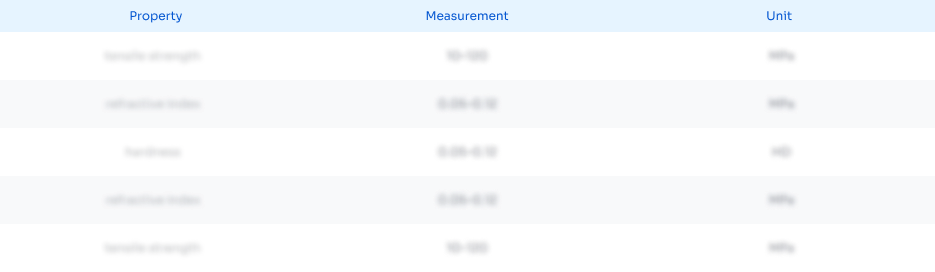
Abstract
Description
Claims
Application Information

- R&D
- Intellectual Property
- Life Sciences
- Materials
- Tech Scout
- Unparalleled Data Quality
- Higher Quality Content
- 60% Fewer Hallucinations
Browse by: Latest US Patents, China's latest patents, Technical Efficacy Thesaurus, Application Domain, Technology Topic, Popular Technical Reports.
© 2025 PatSnap. All rights reserved.Legal|Privacy policy|Modern Slavery Act Transparency Statement|Sitemap|About US| Contact US: help@patsnap.com