Preparation method and application of azo dye adsorbent
A technology of azo dyes and adsorbents, applied in the field of environmental engineering, to achieve the effects of non-toxic materials, convenient preparation, and simple ingredients
- Summary
- Abstract
- Description
- Claims
- Application Information
AI Technical Summary
Problems solved by technology
Method used
Image
Examples
Embodiment 1
[0037] 5g K 2 S 2 o 8 and 5g P 2 o 5 Add it into 20mL of concentrated sulfuric acid, after it is fully dissolved, heat up to 80°C, then add 5g of graphite powder, stop heating after 4 hours of magnetic stirring, and naturally cool to room temperature 15°C; Dilute the obtained product to 5% of the original volume with distilled water times, centrifuge (2000r / min) to collect the precipitate, and wash with distilled water 3 times to obtain pre-oxidized graphite;
[0038] The obtained pre-oxidized graphite was dispersed in 40mL of concentrated sulfuric acid with a mass fraction of 70%, cooled to 0°C in an ice-salt bath, and 10g of KMnO 4 Add it to the pre-oxidized graphite dispersion, react for 1 hour, then add 1120mL distilled water and 20mL hydrogen peroxide, centrifuge (500r / min) to remove impurities, continue to centrifuge the supernatant (4000r / min), collect the precipitate, and obtain graphite oxide (GO).
Embodiment 2
[0040] 10g K 2 S 2 o 8 and 10g P 2 o 5Add it into 30mL of concentrated sulfuric acid, after it is fully dissolved, heat up to 60°C, then add 10g of graphite powder, stop heating after 6 hours of magnetic stirring, and naturally cool the room temperature to 35°C; Dilute the obtained product to 3% of the original volume with distilled water times, centrifuge (4000r / min) to collect the precipitate, and wash with distilled water 4 times to obtain pre-oxidized graphite;
[0041] The obtained pre-oxidized graphite was dispersed in 80mL of concentrated sulfuric acid with a mass fraction of 98%, cooled to -5°C in an ice-salt bath, and 40g KMnO 4 Add to the pre-oxidized graphite dispersion, react for 2 hours, then add a certain amount of 2240mL distilled water and 40mL hydrogen peroxide, centrifuge (500r / min) to remove impurities, and continue to centrifuge the supernatant (6000r / min), collect the precipitate, Graphite oxide A was obtained.
Embodiment 3
[0043] 10g K 2 S 2 o 8 and 10g P 2 o 5 Add it into 40mL of concentrated sulfuric acid, after it is fully dissolved, heat up to 90°C, then add 5g of graphite powder, stop heating after 8 hours of magnetic stirring, and naturally cool to room temperature 25°C; Dilute the obtained product to 10% of the original volume with distilled water times, centrifuged (3000r / min) to collect the precipitate, and washed 5 times with distilled water to obtain pre-oxidized graphite;
[0044] The obtained pre-oxidized graphite was dispersed in 40mL of concentrated sulfuric acid with a mass fraction of 85%, cooled to 0°C in an ice-salt bath, and 40g KMnO 4 Add to the pre-oxidized graphite dispersion, react for 3 hours, then add 2240mL distilled water and 40mL hydrogen peroxide, centrifuge (500r / min) to remove impurities, continue to centrifuge the supernatant (6000r / min), collect the precipitate, and obtain graphite oxide .
PUM
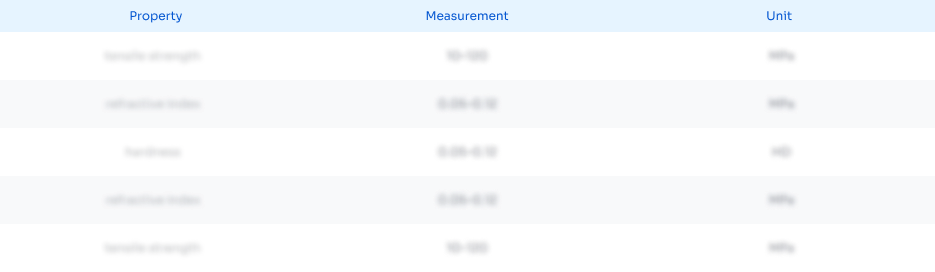
Abstract
Description
Claims
Application Information

- R&D Engineer
- R&D Manager
- IP Professional
- Industry Leading Data Capabilities
- Powerful AI technology
- Patent DNA Extraction
Browse by: Latest US Patents, China's latest patents, Technical Efficacy Thesaurus, Application Domain, Technology Topic, Popular Technical Reports.
© 2024 PatSnap. All rights reserved.Legal|Privacy policy|Modern Slavery Act Transparency Statement|Sitemap|About US| Contact US: help@patsnap.com