Polyesterimide enameled wire enamel and manufacturing method thereof
An enameled wire varnish and polyesterimide technology, which is applied to the enameled wire varnish field, can solve the problems of high cost, expensive solvent and the like of polyimide and polyamideimide, and achieves good freezing resistance, simple production method and low cost. low effect
- Summary
- Abstract
- Description
- Claims
- Application Information
AI Technical Summary
Problems solved by technology
Method used
Image
Examples
Embodiment 1
[0017] Embodiment 1: Polyesterimide wire enamelled varnish, the parts by weight of its raw materials are: 110 parts of xylenol, 100 parts of trimellitic anhydride, 5 parts of maleic anhydride, 50 parts of acrylate, 10 parts of diaminodiphenyl ether , 15 parts of glycerin, 40 parts of ethylene glycol, 1 part of straw ash, 2 parts of tetrabutoxytitanium, 1 part of attapulgite, and 1 part of N-methylpyrrolidone.
Embodiment 2
[0018] Embodiment 2: Polyesterimide wire enamelled varnish, the parts by weight of its constituent raw materials are: 115 parts of xylenol, 105 parts of trimellitic anhydride, 8 parts of maleic anhydride, 55 parts of acrylate, 15 parts of diaminodiphenyl ether , 18 parts of glycerin, 45 parts of ethylene glycol, 2 parts of straw ash, 4 parts of tetrabutoxytitanium, 2 parts of attapulgite, and 1.5 parts of N-methylpyrrolidone.
Embodiment 3
[0019] Embodiment 3: Polyesterimide wire enamelled varnish, the parts by weight of its raw materials are: 120 parts of xylenol, 110 parts of trimellitic anhydride, 10 parts of maleic anhydride, 60 parts of acrylate, 20 parts of diaminodiphenyl ether , 20 parts of glycerin, 50 parts of ethylene glycol, 3 parts of straw ash, 5 parts of tetrabutoxytitanium, 3 parts of attapulgite, and 2 parts of N-methylpyrrolidone.
[0020] The preparation method of polyesterimide wire enamel of the present invention comprises the following steps:
[0021] (1) Add trimellitic anhydride, maleic anhydride and acrylate to the reactor according to the weight of the raw materials, heat to 150-200°C, and react for 4.5-5.5 hours;
[0022] (2) Add diaminodiphenyl ether to the solution obtained in step (1) by weight, keep it at 155-180°C, and keep it warm for half an hour;
[0023] (3) Add ethylene glycol and glycerin to the solution obtained in step (2), heat up to 180-210°C, react for 30-60 minutes, v...
PUM
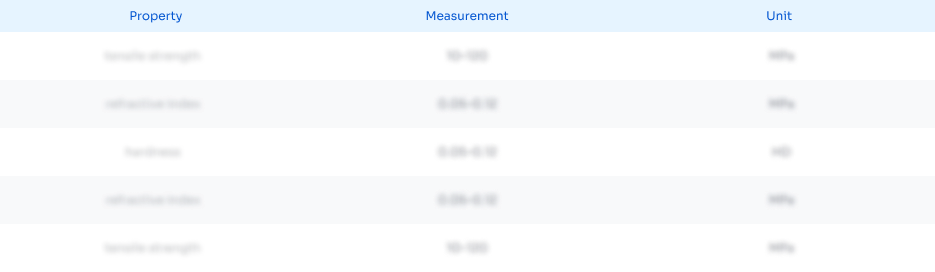
Abstract
Description
Claims
Application Information

- R&D
- Intellectual Property
- Life Sciences
- Materials
- Tech Scout
- Unparalleled Data Quality
- Higher Quality Content
- 60% Fewer Hallucinations
Browse by: Latest US Patents, China's latest patents, Technical Efficacy Thesaurus, Application Domain, Technology Topic, Popular Technical Reports.
© 2025 PatSnap. All rights reserved.Legal|Privacy policy|Modern Slavery Act Transparency Statement|Sitemap|About US| Contact US: help@patsnap.com