Method for preparing hydrogen fluoride and coproducing white carbon black with silicon tetrafluoride
A silicon tetrafluoride, hydrogen fluoride technology, applied in the direction of fluorine/hydrogen fluoride, silicon oxide, silicon dioxide, etc., can solve the problems of poor production safety, difficult filtration, incomplete conversion, etc., achieve huge environmental and social benefits, promote The effect of healthy and sustainable development and superior product quality
- Summary
- Abstract
- Description
- Claims
- Application Information
AI Technical Summary
Problems solved by technology
Method used
Image
Examples
Embodiment 1
[0022] Pass 700kg of crude silicon tetrafluoride gas produced by phosphate fertilizer through a 300-mesh bag filter to remove sodium fluoride dust in the gas, then pass through two-stage activated carbon absorption columns, and the first-stage absorption column is filled under vacuum conditions at 100-300°C Activate the activated carbon for 4 hours, and fill the secondary absorption column with the activated carbon activated for 4 hours under vacuum conditions at 300-700°C. The activated carbon obtained by this method has higher activity and the lowest adsorption water content (2 , O 2 、H 2 , CO and CH 4 etc., the liquefied silicon tetrafluoride enters the reaction of the next procedure through gasification, and obtains 684 kg of silicon tetrafluoride gas whose purity can reach 99.99%.
[0023] Pass 684kg of purified silicon tetrafluoride gas and 245kg of water vapor into the hydrolysis reactor at a rate of 1:2, and carry out the hydrolysis reaction at 300°C; 530kg of crude ...
Embodiment 2
[0025] The thick silicon tetrafluoride gas 1000kg that phosphate fertilizer by-product is purified, purification method is identical with the silicon tetrafluoride purification method among the embodiment 1, and corresponding control condition can be selected arbitrarily within its scope, obtains the tetrafluoride gas that purity can reach 99.99%. Silicon fluoride gas 978kg. Then 978kg of silicon tetrafluoride gas and 337kg of water vapor are passed into the hydrolysis reactor at a rate of 1:2, and the hydrolysis reaction is carried out at 500°C; 750kg of crude hydrogen fluoride gas produced by hydrolysis is first introduced into the dust collector to remove solid impurities such as dust, The dust collector adopts a plate dust collector and a bag dust collector. The hydrogen fluoride gas after dust removal enters the first-stage rectification tower, and the condensation temperature at the top of the tower is controlled at 50°C to condense the hydrogen fluoride and return it to ...
Embodiment 3
[0027]The crude silicon tetrafluoride gas 800kg that phosphate fertilizer by-product is purified, purification method is identical with the silicon tetrafluoride purification method among the embodiment 1, and corresponding control condition can be selected arbitrarily within its scope, obtains the tetrafluoride gas that purity can reach 99.99%. Silicon fluoride gas 785kg. Then 785kg of silicon tetrafluoride gas and 270kg of water vapor are passed into the hydrolysis reactor at a rate of 1:2, and the hydrolysis reaction is carried out at 200°C; 600kg of crude hydrogen fluoride gas produced by hydrolysis is first introduced into the dust collector to remove solid impurities such as dust, The dust collector adopts a plate dust collector and a bag dust collector. The hydrogen fluoride gas after dust removal enters the first-stage rectification tower, and the condensation temperature at the top of the tower is controlled at 30°C to condense the hydrogen fluoride and return it to th...
PUM
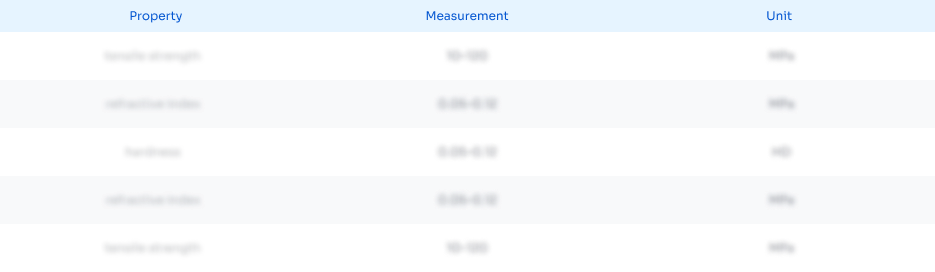
Abstract
Description
Claims
Application Information

- R&D
- Intellectual Property
- Life Sciences
- Materials
- Tech Scout
- Unparalleled Data Quality
- Higher Quality Content
- 60% Fewer Hallucinations
Browse by: Latest US Patents, China's latest patents, Technical Efficacy Thesaurus, Application Domain, Technology Topic, Popular Technical Reports.
© 2025 PatSnap. All rights reserved.Legal|Privacy policy|Modern Slavery Act Transparency Statement|Sitemap|About US| Contact US: help@patsnap.com