Pipe fitting with zinc plated at outer part and plastic coated at inner part as well as production process of same
A production process and technology for plastic pipe fittings, applied in the field of external galvanized internal plastic-coated pipe fittings and its production process, can solve problems such as poor adhesion and easy peeling of the coating, and achieve high production efficiency, product quality assurance, simple and reliable production process Effect
- Summary
- Abstract
- Description
- Claims
- Application Information
AI Technical Summary
Problems solved by technology
Method used
Image
Examples
Embodiment Construction
[0015] An outer galvanized inner plastic-coated pipe fitting comprises an outer galvanized layer 1, a malleable steel part base 2, and an inner layer of polyethylene or epoxy / polyester coating 3.
[0016] The specific production process of the outer galvanized inner plastic-coated pipe fittings is as follows:
[0017] A Sand blasting on the inner wall: Use sand blasting machine equipment to sand blast the inner wall of the pipe fittings to remove the galvanized layer. Note that the outer galvanized layer must not be damaged.
[0018] B Neutral degreasing and decontamination: ① The ratio of slotting chemical solution is 12%. Fill the tank with water until it is 80% full, and add it slowly while stirring. It can be added flexibly according to the degreasing effect and the degree of oil pollution. ②. The processing time is 7 minutes. Clean up the oil on the liquid surface in time. When the tank liquid is seriously dirty and the effect of adding liquid medicine is not obvious...
PUM
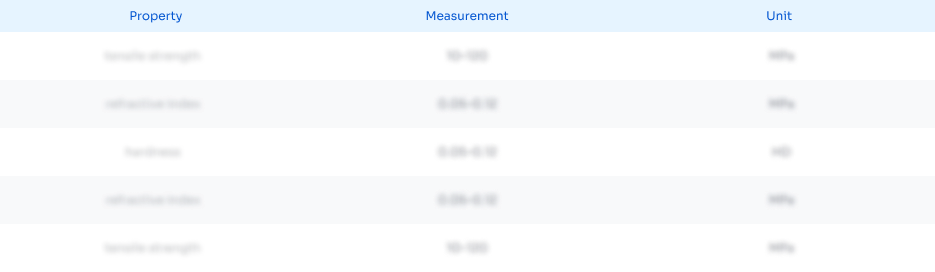
Abstract
Description
Claims
Application Information

- R&D
- Intellectual Property
- Life Sciences
- Materials
- Tech Scout
- Unparalleled Data Quality
- Higher Quality Content
- 60% Fewer Hallucinations
Browse by: Latest US Patents, China's latest patents, Technical Efficacy Thesaurus, Application Domain, Technology Topic, Popular Technical Reports.
© 2025 PatSnap. All rights reserved.Legal|Privacy policy|Modern Slavery Act Transparency Statement|Sitemap|About US| Contact US: help@patsnap.com