Method for removing strained layer on surface of single crystal blade casting through chemical milling
A single crystal blade and strain layer technology is applied in the field of chemical milling to remove the surface strain layer of single crystal blade castings, which can solve the problems of low yield, reduce the probability of the existence of the surface strain layer, reduce the incidence of recrystallization, The effect of preventing recrystallization
- Summary
- Abstract
- Description
- Claims
- Application Information
AI Technical Summary
Problems solved by technology
Method used
Examples
Embodiment 1
[0015] Dissolving sodium hydroxide, sodium carbonate and sodium phosphate in water is prepared into degreasing liquid, the concentration of sodium hydroxide in the degreasing liquid is 10g / L, the concentration of sodium carbonate is 32g / L, and the concentration of sodium phosphate is 18g / L;
[0016] Seal the blade window of the single crystal blade casting with wax, and then place it in a degreasing solution at a temperature of 50±2°C for degreasing, and the degreasing time is 6 minutes;
[0017] Dissolve hydrochloric acid, hydrofluoric acid, nitric acid, acetic acid, ferric chloride and chromic anhydride in water to prepare chemical milling solution. The concentration of hydrochloric acid in the chemical milling solution is 220ml / L, the concentration of hydrofluoric acid is 300ml / L, nitric acid The concentration of acetic acid is 110ml / L, the concentration of acetic acid is 45ml / L, the concentration of ferric chloride is 300g / L, and the concentration of chromic anhydride is 20...
Embodiment 2
[0023] Dissolving sodium hydroxide, sodium carbonate and sodium phosphate in water is prepared into degreasing liquid, the concentration of sodium hydroxide in the degreasing liquid is 11g / L, the concentration of sodium carbonate is 31g / L, and the concentration of sodium phosphate is 19g / L;
[0024] Seal the blade window of the single crystal blade casting with wax, and then place it in a degreasing solution at a temperature of 50±2°C for degreasing, and the degreasing time is 8 minutes;
[0025] Dissolve hydrochloric acid, hydrofluoric acid, nitric acid, acetic acid, ferric chloride and chromic anhydride in water to prepare chemical milling solution. The concentration of hydrochloric acid in the chemical milling solution is 240ml / L, the concentration of hydrofluoric acid is 280ml / L, nitric acid The concentration of acetic acid is 115ml / L, the concentration of acetic acid is 44ml / L, the concentration of ferric chloride is 320g / L, and the concentration of chromic anhydride is 21...
Embodiment 3
[0031] Dissolving sodium hydroxide, sodium carbonate and sodium phosphate in water is prepared into degreasing liquid, the concentration of sodium hydroxide in the degreasing liquid is 12g / L, the concentration of sodium carbonate is 30g / L, and the concentration of sodium phosphate is 20g / L;
[0032] Seal the blade window of the single crystal blade casting with wax, and then place it in a degreasing solution at a temperature of 50±2°C for degreasing, and the degreasing time is 7 minutes;
[0033] Dissolve hydrochloric acid, hydrofluoric acid, nitric acid, acetic acid, ferric chloride and chromic anhydride in water to prepare chemical milling solution. The concentration of hydrochloric acid in the chemical milling solution is 260ml / L, the concentration of hydrofluoric acid is 250ml / L, nitric acid The concentration of acetic acid is 120ml / L, the concentration of acetic acid is 42ml / L, the concentration of ferric chloride is 330g / L, and the concentration of chromic anhydride is 20...
PUM
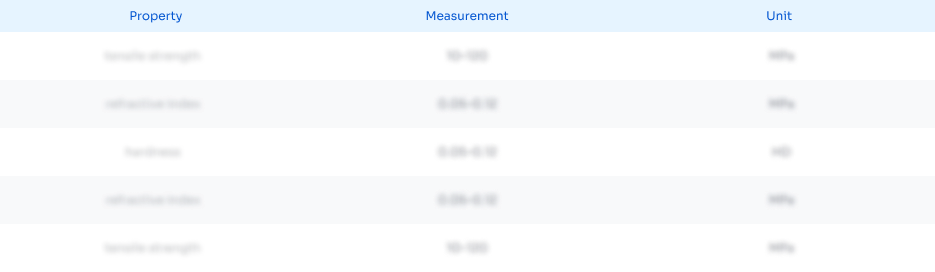
Abstract
Description
Claims
Application Information

- R&D
- Intellectual Property
- Life Sciences
- Materials
- Tech Scout
- Unparalleled Data Quality
- Higher Quality Content
- 60% Fewer Hallucinations
Browse by: Latest US Patents, China's latest patents, Technical Efficacy Thesaurus, Application Domain, Technology Topic, Popular Technical Reports.
© 2025 PatSnap. All rights reserved.Legal|Privacy policy|Modern Slavery Act Transparency Statement|Sitemap|About US| Contact US: help@patsnap.com