Cryogenic treatment method for ceramic/metal ceramic cutting tool
A cryogenic treatment and cermet technology, applied in the field of material heat treatment technology, can solve the problems of easy chipping, lack of systematic research on cryogenic technology, poor strength and toughness of ceramics or cermets, etc., to achieve good heat exchange effect and controllable treatment temperature. , the effect of controllable cooling speed
- Summary
- Abstract
- Description
- Claims
- Application Information
AI Technical Summary
Problems solved by technology
Method used
Examples
Embodiment 1
[0018] Will Al 2 o 3 After cleaning and wiping the ceramic-based knives, put them into a program-controlled cryogenic box, and set the process to start cryogenic treatment. The process is: first drop from room temperature to -100°C, cool at a rate of 1.5°C / min, and keep warm for 1h; then cool down To -150°C, the cooling rate is 2°C / min, and the temperature is kept for 24h. After cryogenic treatment, close the liquid nitrogen input valve and start heating and tempering: the tempering temperature is 100°C, the heating rate is 2°C / min, keep the temperature for 4h, and then cool down to room temperature naturally.
[0019] The cutting tool after the cryogenic process was installed on the machine tool, and the tool test experiment was carried out. The processing material was 35CrMnSiA, and the number of processed workpieces increased from 84 before cryogenic to 124, with an increase rate of 50%.
Embodiment 2
[0021] After cleaning and wiping the Ti(C,N)-based cermet tool, put it into a program-controlled cryogenic box, and set the process to start the cryogenic treatment. The process is: first drop from room temperature to -100°C, and the cooling rate is 1.5°C / min, keep warm for 1h; then cool down to -150℃, cooling rate is 2℃ / min, keep warm for 24h. After cryogenic treatment, close the liquid nitrogen input valve and start heating and tempering: the tempering temperature is 100°C, the heating rate is 2°C / min, keep the temperature for 4h, and then cool down to room temperature naturally.
[0022] The tool after the cryogenic process was installed on the machine tool, and the tool test experiment was carried out. The processing material was 20CrMnTiH, and the processed workpiece was a high-speed synchronizer gear sleeve. is 100%.
PUM
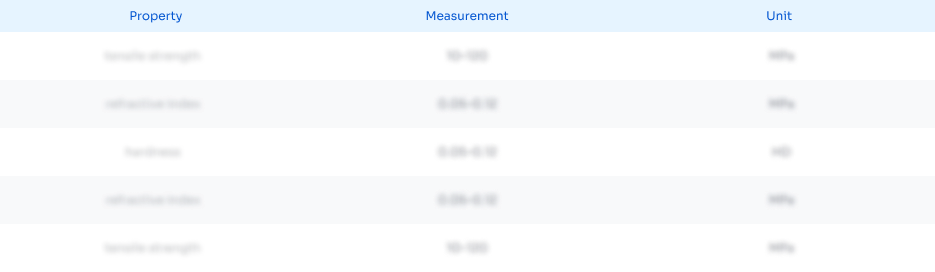
Abstract
Description
Claims
Application Information

- R&D
- Intellectual Property
- Life Sciences
- Materials
- Tech Scout
- Unparalleled Data Quality
- Higher Quality Content
- 60% Fewer Hallucinations
Browse by: Latest US Patents, China's latest patents, Technical Efficacy Thesaurus, Application Domain, Technology Topic, Popular Technical Reports.
© 2025 PatSnap. All rights reserved.Legal|Privacy policy|Modern Slavery Act Transparency Statement|Sitemap|About US| Contact US: help@patsnap.com